ACS: Ultra-thin MXenepolymer coated fabric with alternating structure for enhancing electromagnetic interference shielding and fire protection performance
QQ Academic Group: 1092348845
Detailed
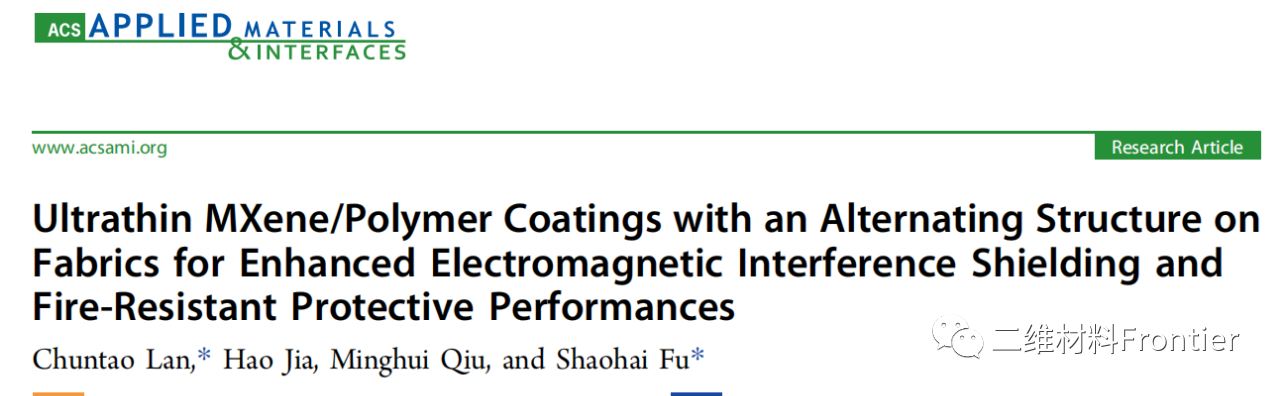
1. Article overview
With the rapid development of electronic equipment and wireless communications, wearable electromagnetic interference EMI shielding fabrics have become popular. Among them, electromagnetic pollution is a major issue for human health and the reliability of precision equipment. Since the requirements for coating thickness are usually opposite, the balance between EMI shielding efficiency SE and fabric flexibility remains challenging. The author prepares MXene/insulating polymer coatings with alternating structures through a step-by-step assembly technique, combining excellent shielding elements, reasonable structures and high nano-filler content. Due to this new strategy, the coating has a nanometer-level thickness ~500 nm that meets the commercial requirements of EMI SE, and well maintains the flexibility and breathability of the fabric. Compared with the corresponding pure MXene coating, this multilayer coating shows a 138.95% EMI SE enhancement due to improved dielectric properties and strong multiple reflections of electromagnetic waves. In addition, this hybrid coating can also act as an excellent fire barrier for internal flammable fabrics, protecting humans and electronic equipment in the event of an accidental fire.
Two, graphic guide
With the rapid development of electronic equipment and wireless communications, wearable electromagnetic interference EMI shielding fabrics have become popular. Among them, electromagnetic pollution is a major issue for human health and the reliability of precision equipment. Since the requirements for coating thickness are usually opposite, the balance between EMI shielding efficiency SE and fabric flexibility remains challenging. The author prepares MXene/insulating polymer coatings with alternating structures through a step-by-step assembly technique, combining excellent shielding elements, reasonable structures and high nano-filler content. Due to this new strategy, the coating has a nanometer-level thickness ~500 nm that meets the commercial requirements of EMI SE, and well maintains the flexibility and breathability of the fabric. Compared with the corresponding pure MXene coating, this multilayer coating shows a 138.95% EMI SE enhancement due to improved dielectric properties and strong multiple reflections of electromagnetic waves. In addition, this hybrid coating can also act as an excellent fire barrier for internal flammable fabrics, protecting humans and electronic equipment in the event of an accidental fire.
Two, graphic guide
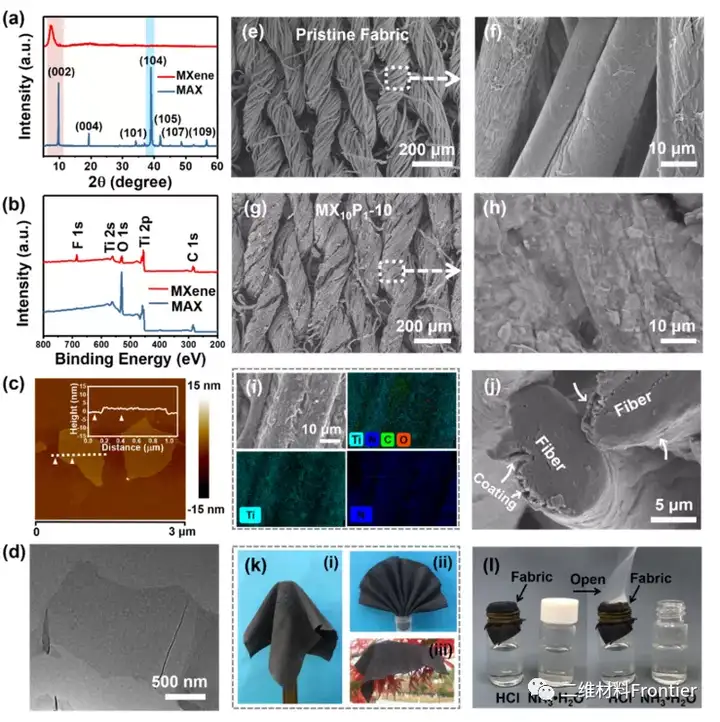
Figure 1. Characterization of MXene flakes and coated fabrics. XRD showed that the penguin aluminum layer was successfully removed and MXene was synthesized. XPS showed that MXene with rich surface chemistry was successfully prepared Figure 1b The MXene obtained by AFM shows a typical flake morphology, and the thickness of the flake is ~1.7 nm. In addition, from the transmission electron microscope TEM image Figure 1d, the lateral size of the plates can be up to a few microns and the presence of wrinkles can infer the flexibility of these plates. The cotton fabric as the MXene/PEI coating substrate shows a knitted structure in the SEM image in Figure 1e. The surface morphology of the original fiber has some wrinkles, which is a typical feature of natural cotton fiber Figure 1f. After being modified by MXene/PEI coating, the fabric can still retain the original knitted structure of the fabric Figure 1g. Due to the unique 2D structure of the MXene board, the hybrid coating mainly covers the fiber surface and partially fills the gaps between adjacent fibers Figure 1h. In Figure 1i, the representative Ti element derived from MXene and the nitrogen N element derived from PEI are uniformly distributed in the fiber direction. There was no significant accumulation of MXene or PEI, which strongly indicates the unique advantages of the step-by-step assembly technology in the preparation of uniform coatings. For MX10P1-10, the coating is wrapped on the inner cotton fiber, and its thickness is just nanometers. As shown in the cross-sectional image of the coated fiber in Figure 1j, the thickness of the coating is ~500 nanometers. This thin coating, coupled with MXenes special 2D structure, ensures that the fabric prepared has excellent flexibility and lightness. The coated fabric has good drape Figure 1k, foldability Figure 1k and light weight Figure 1k
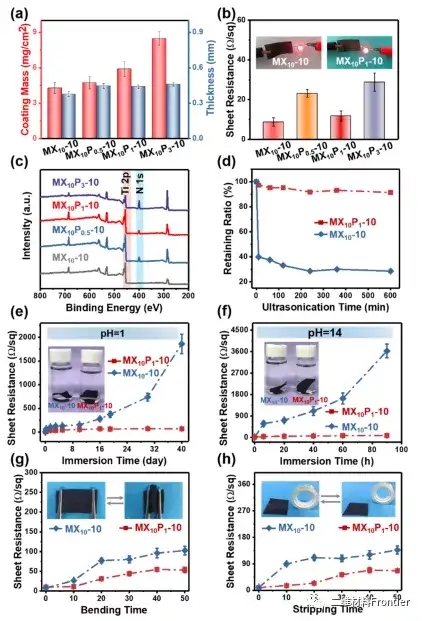
Figure 2. Sheet resistance and stability of coated fabrics. The coating quality of the coated fabric gradually increases with the increase of the PEI concentration Figure 2a. The coating quality of MX10P3-10 is 8.47±0.57 mg/cm2. As shown in Figure 2b, the surface resistance of MX10-10 is 8.68±2.12Ω/sq lower than that of MXene/PEI coated fabric. The better conductivity of MX10-10 is mainly due to the lack of an insulating PEI layer in the coating. After adding PEI, the tensile strength of the modified fabric is slightly improved. However, the tensile strength of MXene/PEI modified fabric does not increase with the increase of PEI concentration. Specifically, the sheet resistance of MX10P1-10 11.75±2.56Ω/sq is smaller than MX10P0.5-10 23.11±1.98Ω/sq and MX10P3-10 28.72±4.57Ω/sq. As shown in Figure 2d, the pure MXene coating ie MX10-10 lost a large amount of ingredients, only 37.5% was retained after 10 minutes before the ultrasonic treatment. With the prolongation of the ultrasonic time, the quality of the MX10-10 coating deteriorated, and only remained at 28.5% after 600 minutes. As shown in Figure 2e, the sheet resistance of MX10P1-10 increased slightly, from 8.20±2.52Ω/sq at the beginning to 68.55±12.17Ω/sq after immersing in HCl solution for 40 days. On the contrary, the sheet resistance of MX10-10 after 40 days of soaking increased from 7.54±1.28Ω/sq at the beginning to 1860±205Ω/sq. As shown in Figure 2g, the sheet resistance of MX10-10 8.07±1.12Ω/sq and MX10P1-10 9.83±1.02Ω/sq are similar at the beginning, and the average sheet resistance of MX10P1-10 after 50 bending cycles Slightly increased to 53.60Ω/sq, the average sheet resistance of the MX10-10 is 102.70Ω/sq. Similarly, the sheet resistance of MX10P1-10 slowly decreases. After 50 peel cycles, the resistance of MX10-10 increases to 66.62Ω/sq, while the resistance of MX10-10 increases to 137.10Ω/sq.
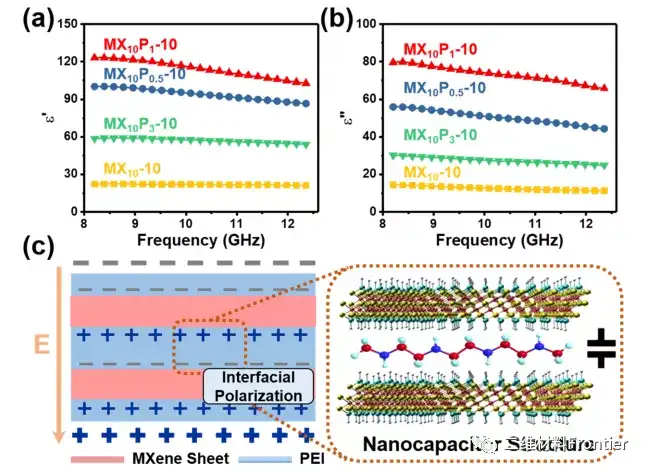
Figure 3. Detection of CYFRA21-1. The complex permittivity of the modified fabric is shown by the real part the polarization capacity of the dielectric layer in Figure 3a and the imaginary part , a measure of dielectric loss in Figure 3b, showing the pure MXene coated fabric It shows relatively low complex permittivity, namely . This dielectric constant is mainly caused by the polarization of surface functional groups and defects in the MXene film under the action of an electric field. After embedding PEI into the MXene coating, both and increase. In the alternating MXene/PEI coating, the PEI layer separates the two adjacent MXene layers to construct a nanocapacitor structure, where the adjacent MXene sheets act as electrodes and PEI acts as a thin dielectric layer, as shown in the right panel in Figure 3c Shown.
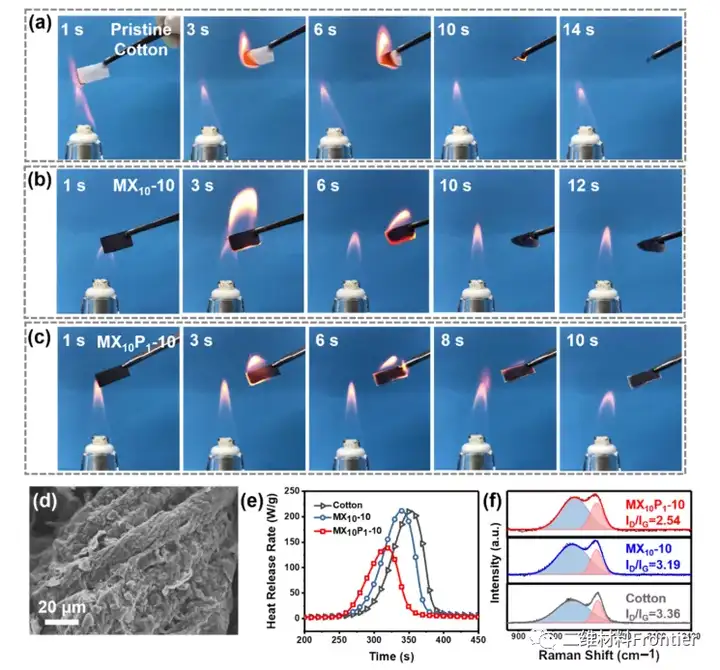
Figure 4. Fire resistance of coated fabrics. As shown in Figure 5a, for the pure cotton fabric, the sample ignites rapidly, burns violently, and continues to burn until the fabric is completely exhausted at 14 seconds. After applying MXene, the fabric was taken out of the flame and burned for 12 seconds, and then extinguished Figure 5b. The MXene/PEI coating gives the fabric a shorter burning time ie 10 seconds Figure 5c . It is worth noting that, as shown in the SEM image in Figure 5d, the fabric and fiber structure are well maintained. It is worth noting that, MX10P1-10 effectively protects MXene and PEI from the effects of flames, and retains the original fabric structure well. The better fire resistance of MX10P1-10 is attributed to the synergistic effect of flame retardants, in view of the good fire resistance of MXene and PEI. The obtained heat release rate curve is shown in Figure 5e. These HRR curves all show a peak. After the coating is introduced, the peak HRR and PHR temperature of the fabric are reduced. In addition, the total heat release of MX10P1-10 is 8.4 kJ/g, which is lower than that of MX10-10 and the original fabric , correspondingly reduced by 21.50% and 34.88%.
3. Full text summary
The author designed the MXene/PEI coated fabric, which has good flexibility and stability, and can effectively shield EMI and flame retardant. After introducing inert PEI molecules, the MXene/PEI coating has achieved good stability under various chemical corrosion and mechanical damage. The alternating structure of MXene/PEI coating significantly improves the dielectric properties of the modified fabric and triggers multiple reflections of incident electromagnetic waves. The electromagnetic interference intensity of the nanocomposite coating thickness reaches 20.13 decibels, and the fabrics good flexibility and air permeability are well maintained. At the same time, MXene/PEI coated cotton fabric has good flame retardant properties. This work provides new insights for the reasonable design of conductive materials with high EMI.
Article link: https://pubs.acs.org/doi/10.1021/acsami.1c11638.
This information is sourced from the Internet for academic exchanges only. If there is any infringement, please contact us to delete it immediately.
3. Full text summary
The author designed the MXene/PEI coated fabric, which has good flexibility and stability, and can effectively shield EMI and flame retardant. After introducing inert PEI molecules, the MXene/PEI coating has achieved good stability under various chemical corrosion and mechanical damage. The alternating structure of MXene/PEI coating significantly improves the dielectric properties of the modified fabric and triggers multiple reflections of incident electromagnetic waves. The electromagnetic interference intensity of the nanocomposite coating thickness reaches 20.13 decibels, and the fabrics good flexibility and air permeability are well maintained. At the same time, MXene/PEI coated cotton fabric has good flame retardant properties. This work provides new insights for the reasonable design of conductive materials with high EMI.
Article link: https://pubs.acs.org/doi/10.1021/acsami.1c11638.
This information is sourced from the Internet for academic exchanges only. If there is any infringement, please contact us to delete it immediately.
- Previous: Liu Yang/Kang Chunshen
- Next: A Rising 2D Star: Nove