New class of two-dimensional materials: check the highlights of MXene applied to flexible sensing material devices
QQ Academic Group: 1092348845
Detailed
1. Science Advance: MXenes pushes hydrogel sensing performance to new limits
With the rapid development of technologies such as wearable electronics, real-time detection and soft robotics, strain sensors are required to have high sensitivity, stretchability, adherence to arbitrarily complex surfaces, and preferably self-repairing. . Conductive hydrogels are considered ideal sensing materials for these applications. However, their sensitivity is generally low, and due to their viscoelasticity, they cause signal lag and fluctuations, which may affect their sensing performance. Researchers at King Abdullah University of Science and Technology have developed a conductive hydrogel "MXenes stretch hydrogel sensor performance to new limits" and published it on the international journal Science Advance. It makes the e-skins stretch ability, self-healing ability and The strain sensitivity has reached a new limit. This is a hydrogel composite material mixed with MXene (Ti3C2Tx). The sensing performance of this hydrogel is better than that of previously reported hydrogel strain sensors. The resulting composite hydrogel (MXene hydrogel (M-hydrogel)) shows excellent tensile strain sensitivity with a measurement factor (GF) of 25, which is ten times that of the original hydrogel. In addition, M-hydrogel exhibits super-stretchability of more than 3400%, rapid self-healing ability, excellent compliance, and adhesion to various surfaces including human skin. The M-hydrogel composite shows higher sensitivity under compressive strain (GF=80) than under tensile strain. The use of this asymmetric strain sensitivity combined with viscous deformation (self-healing residual deformation) adds a new dimension to the hydrogels sensing capabilities. Therefore, the direction and speed of movement on the surface of the hydrogel can be easily detected. Based on this effect, M-hydrogel shows excellent sensing performance in advanced sensing applications.
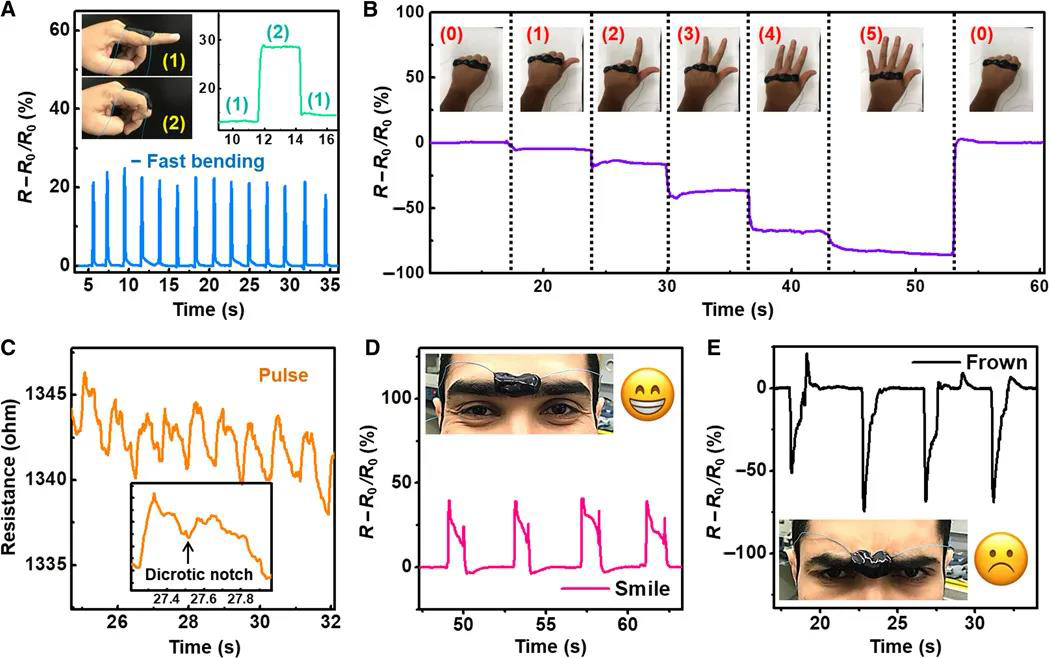
Figure 1. General sensing performance of M-hydrogel. (A to E) The resistance change of M hydrogel in response to (A) finger bending, (B) different gestures, (C) pulse and (D and E) facial expressions.
Literature link: http://advances.sciencemag.org/content/4/6/eaat0098
2. AFM: conductive, self-healing, antifreeze MXene organic hydrogel, used for flexible strain sensors
Flexible wearable strain sensors are widely used in electronic skin, medical care monitoring and human-computer interaction, and have attracted much attention. At present, conductive hydrogel has become an ideal material for the preparation of flexible strain sensors due to its excellent electrical conductivity, mechanical tunability and excellent biological properties. Conventional conductive hydrogels using pure water as a dispersant freeze at zero degrees, thereby limiting ion migration and severely limiting their applications at low temperatures. Even at room temperature, the water content of the hydrogel will inevitably evaporate, hindering long-term stability and durability. Therefore, the development of conductive hydrogel sensors with frost resistance, water retention and long-term stability has become a hot spot in current research. Wan Pengbo of Beijing University of Chemical Technology and Yu Guihua of the University of Texas at Austin published a paper "Conductive MXene Nanocomposite Organo hydrogel for Flexible, Healable, Low-Temperature Tolerant Strain Sensors" in the international journal Advance Functional Materials. The gel (MNH) is immersed in an ethylene glycol (EG) solution to replace part of the water, thereby developing a conductive, antifreeze and self-healing MXene nanocomposite organic hydrogel (MNOH). MNH was prepared by embedding conductive MXene nanosheets into a hydrogel polymer network. The prepared MNOH has strong frost resistance under extreme temperature (−40°C) and has long-lasting water retention (8d). Thanks to the dynamic cross-linking between the PVA hydroxyl and tetrahydroxyborate ions and the supramolecular interaction between EG, PVA and MXene, MNOH has excellent self-repair capabilities. In addition, MNOH can detect human activities with a wide strain range (up to 350% strain) and high sensitivity (GF = 44.85) in real time at extremely low temperatures (−40°C). This work demonstrates the great potential for artificial skin, soft robots, and human-machine interfaces at extremely low temperatures.
Figure 1. a) Schematic diagram of the preparation of conductive, antifreeze and self-repairing MNOH. b) SEM of layered MXene flakes and d) lyophilized MNH.
Literature link:
https://doi.org/10.1002/adfm.201904507.
3. ACS Nano: protein-inspired self-repairing MXene/rubber-based supramolecular elastomer for smart sensing
In recent years, flexible electronic sensors have shown broad application prospects in healthcare, smart robots, wearable electronic devices, and human-computer interaction, and have attracted widespread attention. However, electronic sensors are prone to unavoidable scratches, cracks, and breaks during continuous deformation, which can cause performance degradation. Therefore, devoting to the development of flexible sensors with self-healing properties is essential for extending life and reliability. Despite the remarkable achievements, these sensors still require external stimuli (heat, solvent, light) in the healing process, and the mechanical properties of the recovered sensors are poor, which limits their practical application. It is still a huge challenge to design an autonomous self-repairing electronic sensor with improved mechanical properties and excellent self-repair efficiency. Professor Lu Canhui and Zhou Zehang of Sichuan University reported on a protein-inspired self-healing MXene/rubber-based supramolecular elastomer for intelligent sensing. The work "Protein-Inspired Self-Healable Ti3C2 MXenes/ Rubber-Based Supramolecular Elastomer for Intelligent Sensing" was published in the international journal ACS Nano. The MXene nanosheets modified with serine through esterification reaction are assembled with the elastomer matrix to form a fine dynamic supramolecular hydrogen bond interface. Nanostructured MXenes/rubber-based supramolecular elastomers (NMSE) have ideal recovery toughness (12.34 MJ/m3), excellent self-healing properties (~100%), high specification factor (107.43), low strain detection limit at room temperature (0.1%) and fast response time (50 ms), which can accurately detect the subtle movements of the human body (including voice, facial expressions, pulse and heartbeat) and even changes in moisture after the cutting/repair process. In addition, the NMSE-based sensor integrated with a complete signal processing system shows great feasibility in voice-controlled motion, which shows broad prospects in future wearable electronic devices and soft intelligent robots.
Figure 1. The main preparation process of NMSE. (A) Surface modification of MXene nanosheets with serine through esterification reaction. (B) Construct a nanostructured MXene network in NMSE by latex assembly method.
Literature link: https://dx.doi.org/10.1021/acsnano.9b09802
4. Nano Energy: 3D Mxene-sponge network and its application in piezoresistive sensors
With the rapid development of wearable electronic devices, flexible pressure sensors have received widespread attention due to their potential applications in motion detection, biomedical monitoring, and human-computer interaction. However, most flexible pressure sensors require well-designed nanostructures, and the preparation process is time-consuming and labor-intensive. Therefore, there is an urgent need for large-scale and low-cost technology to manufacture flexible pressure-sensitive materials with high sensitivity in a large pressure range. The research group of Associate Professor Liu Nishuang of Huazhong University of Science and Technology successfully published the paper "3D hybrid porous Mxene-sponge network and its application in piezoresistive sensor" in the international energy journal Nano Energy. The first author of the paper is Yue Yang. This work produced MXene sponge through a simple and effective dip coating process and applied it to a piezoresistive sensor with insulated polyvinyl alcohol (PVA) nanowires as spacers. The sensor based on MXene sponge has high sensitivity in a wide pressure range (147 kPa-1 for the area less than 5.37 kPa, 442 kPa-1 for the area 5.37-18.56 kPa), detection limit of 9 Pa, Fast response time of 138 milliseconds and excellent durability in 10,000 cycles. The MXene sponge sensor can monitor human physiological signals (such as respiration, joint movement and pulse) in real time. Therefore, the sensor prepared by this method has great potential in measuring pressure distribution and human-computer interaction.
Figure 1. a) Schematic diagram of the manufacturing process of MXene sponge; b, c) Schematic diagram of the manufacturing of sensors based on MXene-Sponge / PVA NWs.
Literature link:
https://doi.org/10.1016/j.nanoen.2018.05.020
5. Advance Functional Materials: Wearable strain-sensing textiles based on highly stretchable MXene/PU fibers
Integrating nanomaterials with high conductivity into stretchable polymer fibers can realize some novel functions, such as strain sensing. The conductivity of 2D MXene exceeds other solution-treated nanomaterials, and it is an ideal material for the production of conductive and stretchable fibers. However, it is a huge challenge to ensure the stretchability in the polymer fiber while imparting conductivity. This is because the introduction of conductive fillers usually leads to a decrease in spinnability (ability to form fibers) or lower stretchability of fibers, so it is not suitable for strain sensing applications. Dr. Shayan Seyedin, Yury Gogotsi and Deakin University Professor Joselito M. Razal (co-corresponding author) published "MXene Composite and Coaxial Fibers with High Stretchability and Conductivity for Wearable Strain Sensing Textiles" in the international journal Advance Functional Materials paper. This work reports a MXene/polyurethane (PU) composite fiber that has both conductivity and high stretchability prepared by wet spinning technology. It is proved that the conductivity at a very low permeation threshold ≈1wt% is lower than the previously reported value of MXene-based polymer composites. When used as a strain sensor, the MXene/PU composite fiber shows a high strain factor of approximately 12900 (approximately 238 at 50% strain) and a larger sensing strain of 152%. The wet spinning process produces fibers with MXene/PU sheath and pure PU, which can further improve the cyclic strain sensing performance. Using a commercial-scale knitting machine, weaving MXene/PU fibers into a one-piece elbow cover can detect various movements of the wearers elbow. This study explains the basic mechanism of the action of MXene in elastomer composites, and proposes a new type of MXene-based fiber and textile strain sensing strategy.
Figure 1. a) Schematic diagram of the spinning process of MXene/PU fiber, b) Digital photo of MXene/PU fiber spinning at ≈9.1wt% MXene to ≈100 m length using IPA coagulation, c) Load and spin on various MXene SEM image of MXene/PU fiber produced under silk condition.
Literature link:
https://doi.org/10.1002/adfm.201910504.
With the development of science and technology, flexible wearable pressure sensors have attracted much attention due to their portability and good biocompatibility. The development of wearable flexible pressure sensors is of great significance in electronic skin, biomedicine, human-computer interaction and health monitoring. We not only require accurate pressure sensing capabilities, but also in flexibility, detection range, stability, and Resilience and other aspects put forward higher requirements for it. The materials currently used in wearable flexible sensors mainly include metal nanoparticles, nanowires, nanosheets, graphene, carbon nanotubes and other substances. Although these materials have good flexibility, their limited deformation ability and large hysteresis behavior limit Their application. The team of Associate Professor Wang Lili of Jilin University and the team of Researcher Shen Guozhen of the Institute of Semiconductors of the Chinese Academy of Sciences have jointly developed a sensor layer material with a bionic interconnect structure. Based on this, the flexible sensor made can make up for the above-mentioned defects. Inspired by human skin, the research team combined natural sea urchin-like microcapsules and two-dimensional MXene nanosheets into a composite film, and introduced a bionic interconnect structure into it. Studies have found that when the film is subjected to external forces, this structure can effectively adjust the stress distribution in the composite film, avoiding the film cracking due to strain concentration, thereby improving the mechanical properties of the material. At the same time, the researchers also used finite element modeling and analysis to prove that the composite film with interconnected structure exhibits stronger deformability compared with the flat film without biomimetic structure, as shown in Figure 1. The experimental results show that the effective elastic modulus of the composite biofilm is 0.73 MPa, which is smaller than the elastic modulus of the original flat film 2.19 MPa, which proves that the three-dimensional
The interconnect structure enhances the deformability of the film.
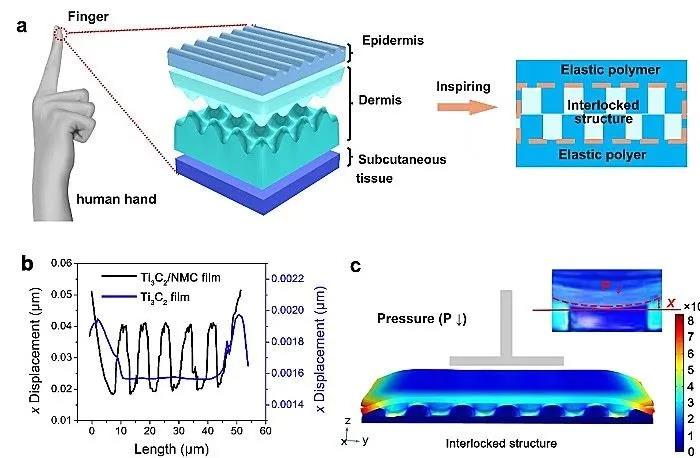
Figure 1. Interconnect structure and finite element analysis
Literature link: DOI: 10.1021/acsnano.9b03454
7. Nano Energy: Highly sensitive and large strain wearable sensor based on MXene/graphene composite film
There is an urgent need for strain sensors with high sensitivity and wide-range linear response. This article introduces the spontaneously formed Ti3C2Tx/graphene/PDMS layered structure, which can be divided into two layers after stretching: a brittle upper layer dominated by Ti3C2Tx and a flexible graphene/PDMS composite bottom layer. The coordinated movement of the upper and lower layers breaks and maintains the balance between the conductive paths, ensuring that the sensor has a high and stable gauge factor in a wide strain range (for example, the strain range is 0–52.6% and 52.6–74.1% when the strain The coefficients are 190.8 and 1148.2). The strain sensor based on Ti3C2Tx/graphene/PDMS layered structure also has a low detection limit (~0.025%), high linearity (R2> 0.98), high cycle stability (more than 5000 cycles) and resistance to all-round human motion Accurate monitoring. Different breathing patterns in yoga have been distinguished to prove the practicality of the sensor.
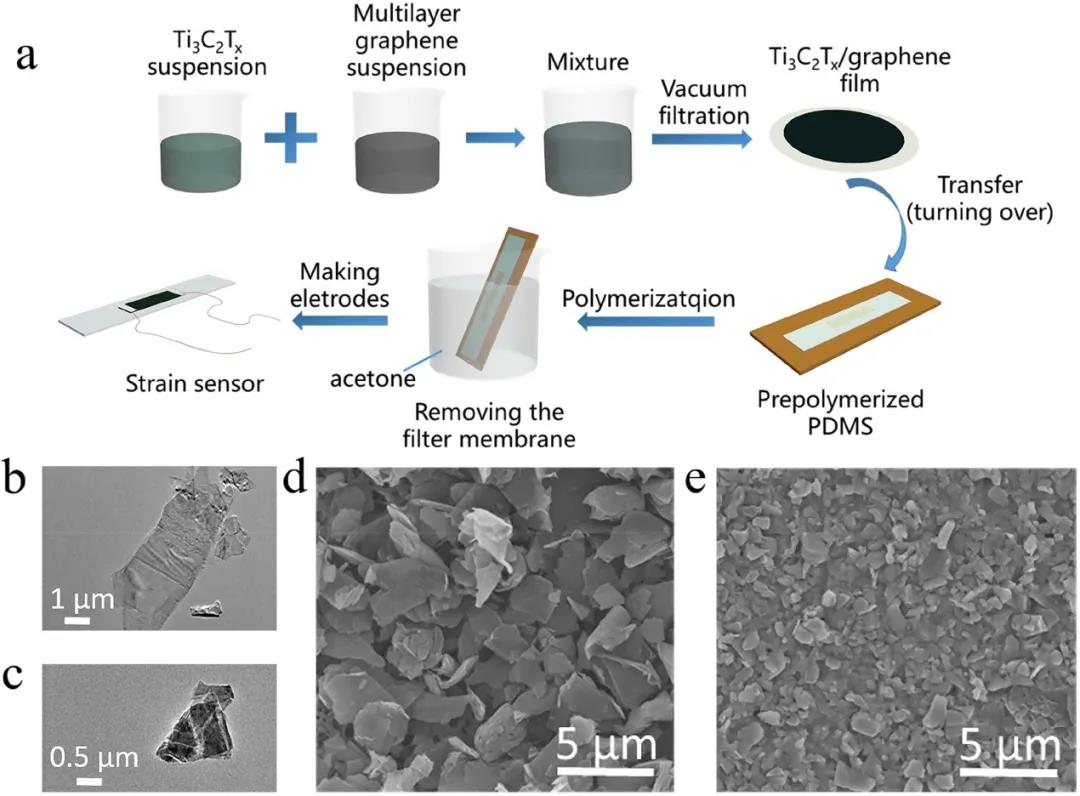
Figure 1. a) Schematic diagram of the fabrication of Ti3C2Tx/graphene strain sensors; b) TEM images of multilayer graphene and c) Ti3C2Tx; d) multilayer graphene and e) overhead SEM images of Ti3C2Tx film.
Related research results were published in Nano Energy (https://doi.org/10.1016/j.nanoen.2019.104134) by the Ranran Wang group of the Chinese Academy of Sciences in 2019. Original: Ti3C2Tx MXene-graphene composite films for wearable strain sensors featured with high sensitivity and large range of linear response.
Electronic skin (E-skin) has similar functions to human skin, including stretchability, self-repair and multi-functional sensory, and has potential applications in personalized medicine, artificial intelligence equipment, and soft robotic systems. Among a variety of soft sensors used in electronic skin, strain sensors are crucial, as they can convert mechanical stimuli into readable signals. Strain sensors can be divided into piezoresistive, capacitive and piezoelectric. Piezoresistive and piezoelectric strain sensors have high sensitivity, but capacitive sensors have low hysteresis, extraordinary stability and high linearity, which are ideal in practical applications, such as blink monitoring, pulse detection and human movement Monitoring covers both small and large strain ranges. The Fuzhen Xuan research group of East China University of Science and Technology published a research paper entitled "Highly Stretchable and Self-Healable MXene/Polyvinyl Alcohol Hydrogel Electrode for Wearable Capacitive Electronic Skin" in the international journal Advanced Electronic Materials. In this research, a self-healing MXene/PVA hydrogel-based electrode was used to develop a capacitive strain sensor with high stretchability, high linearity and small hysteresis. Therefore, MXene is used as a nanofiller incorporated into PVA hydrogel: (1) Enhance the electrical conductivity of the hydrogel. (2) Mixing with PVA improves self-healing. MXene/PVA hydrogel is prepared by directly mixing MXene flakes with a homogeneous PVA solution, and adding a borate solution to complete the gelatinization. Compared with CNT/PVA hydrogel, the synthesized MXene/PVA hydrogel has the breaking elongation (≈1200%), rapid self-healing ability (≈0.15s) and excellent electrical conductivity. Using MXene/PVA hydrogel as the electrode, and using the VHB membrane (4905, 3M) as the dielectric layer, the capacitive strain sensor was assembled into a sandwich structure. The capacitive sensor based on MXene/PVA has good linearity, self-healing and high mechanical durability (relative capacitance change after 10,000 cycles is reduced by 5.8%), and the gauge factor (GF) is about Is 0.4%. High performance enables the device to detect external stimuli (such as joint movement and vocalization), and demonstrate its potential application value in electronic skin.
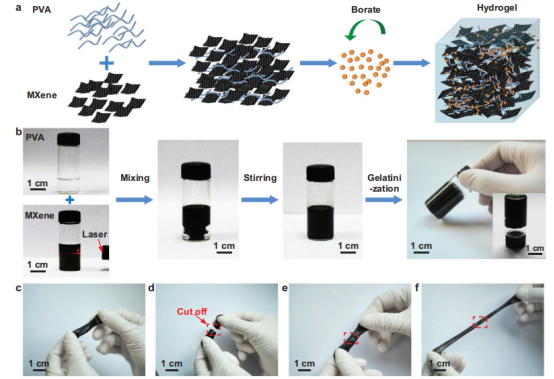
Figure 1. Preparation of MXene/PVA hydrogel. a) Schematic diagram of the synthesis of MXene/PVA hydrogel. b) The photo of the preparation process of MXene/PVA hydrogel. c–f) Photos of self-healing and stretchability of the prepared MXene/PVA hydrogel.
Literature link:
https://doi.org/10.1002/aelm.201900285.
In recent years, the trend towards wearable and miniaturized electronic devices has promoted the development of flexible electronics. At present, the development of wearable strain sensors with both large stretchability (strain> 55%) and high sensitivity (strain coefficient> 100) is still a huge challenge. Drawing inspiration from nature, mother-of-pearl shows excellent mechanical properties, especially both high strength and toughness. This is partly due to its exquisite layered structure and rich interface interaction, which brings great influence to the design of materials. Great inspiration. The research group of Yongsheng Chen and Jiajie Liang of Nankai University published a research paper entitled "Bioinspired Ultrasensitive and Stretchable MXene-Based Strain Sensor via Nacre-Mimetic Microscale "Brick-and-Mortar" Architecture" in the internationally renowned journal ACS Nano. A strain sensor with a pearl-like miniature "brick house" architecture is reported, which can simultaneously achieve ultra-high sensitivity and large stretchability, while at the same time outstanding performance in linearity, reliability, long-term durability and adjustability. This bio-inspired sensor shows a gauge factor greater than 200 in the working strain range of up to 83%, and achieves a high gauge factor of more than 8700 in the strain range of 76-83%. This successful combination of high sensitivity and high stretchability is attributable to (1) the two-dimensional layered structure, which is derived from the combination of MXene/1D silver nanowire "brick" and PDA/Ni2+ "mortar", and ( 2) The synergistic toughening effect produced by the interface interaction between hydrogen bonds and coordination bonds, interlayer sliding and molecular chain stretching. The synergistic behavior of "brick" and "mortar" can not only control the generation of cracks, thereby having higher sensitivity, but also consume a large amount of loading energy, thereby promoting the gradual expansion of cracks during stretching, thereby ensuring significant Comprehensive sensing performance. In addition, this biologically-inspired strain sensor is used to monitor human activities in different motion states to prove its feasibility in a wearable, large-strain human health and motion monitoring system.
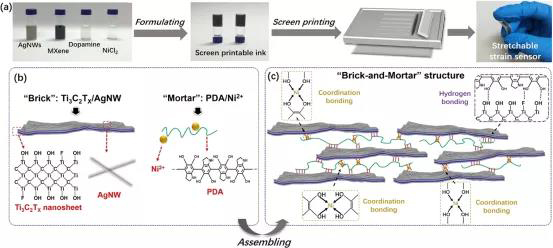
Figure 1. (a) Schematic diagram of the manufacturing process of the bioinspired Ti3C2Tx-AgNW-PDA/Ni2+ sensor manufactured by the screen printing method. (B) Schematic diagram of the structure of "brick" materials (Ti3C2Tx and AgNWs) and "mortar" materials (PDA/Ni2+). (C) Schematic diagram of Ti3C2Tx-AgNW-PDA/Ni2+ sensor based on "physical store" architecture. The interface interaction between Ti3C2Tx-AgNW and PDA/Ni2+ includes hydrogen and coordination bonds.
Literature link: DOI: 10.1021/acsnano.8b07805.
- Previous: Adv.Mater.: MXene ink
- Next: MXene breakthrough: Na