Hydrogel heart that can
QQ Academic Group: 1092348845
Detailed
Many biological tissues, such as the heart and vocal cords, generally work through complex shapes, and they also have ultra-high fatigue resistance to ensure long-term stable operation (the heart beats about 3 billion times in a persons life). Researchers have been able to synthesize hydrogels to simulate soft biological tissues and realize applications in tissue repair, regenerative medicine, and soft robotics. However, synthetic hydrogels are different from biological tissues and are prone to fatigue fracture. Associate Professor Tang Jingda of Xian Jiaotong University and the team of Academician Suo Zhigang of Harvard University successfully prepared a heterogeneous hydrogel with the shape of a heart valve through the stereolithography-casting method. This kind of hydrogel is composed of a skeleton and a matrix. Both hydrogels are elastic and stretchable, but their modulus is very different. Their polymer networks form a topological entanglement structure, with good adhesion at the interface, and fatigue threshold. Up to 400J/m2. The research results were published on "Matter" with the title Fabricating hydrogels to mimic biological tissues of complex shapes and high fatigue resistance.
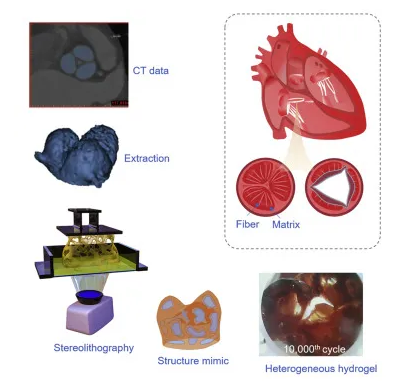
[Structural design and preparation of hydrogels] In order to obtain high fatigue resistance, the two hydrogels should have large modulus contrast and strong adhesion at the interface. The carboxyl-Fe 3+ complex-reinforced polyacrylamide-polyacrylic acid (PAAm-PAA) hydrogel is used as the backbone, and its modulus is about 1 MPa. In addition, PAAm hydrogel is selected as the soft matrix, with a modulus of 0.01-0.1 MPa. As shown in the figure below, a variety of different shapes of hydrogel skeletons can be manufactured by stereolithography.
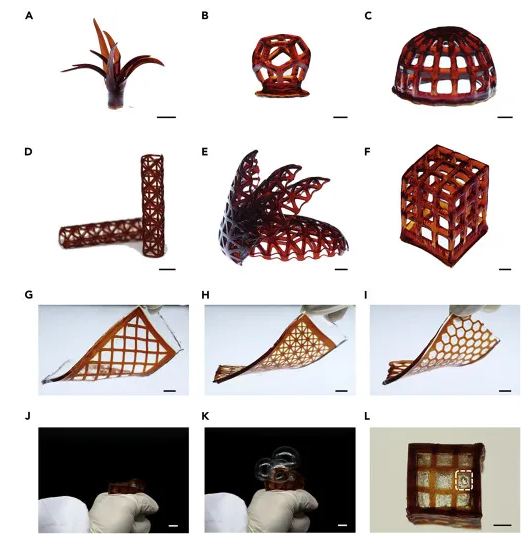
Place the completed skeleton in a mold, and inject the PAAm precursor to polymerize the soft hydrogel matrix. The hydrogel precursor easily migrates into the polymer network of the backbone, so the soft matrix and the polymer network of the backbone will form a topologically entangled structure. A thin layer of soft matrix can be poured on the surface of the hollow cube to obtain the framework-matrix composite material. When the cube is extruded, it will bulge a little (J), suddenly expand (K), or even randomly due to the presence of air. The position is broken (L), which shows that the airtightness of the composite cube is very good, as shown in the figure below.
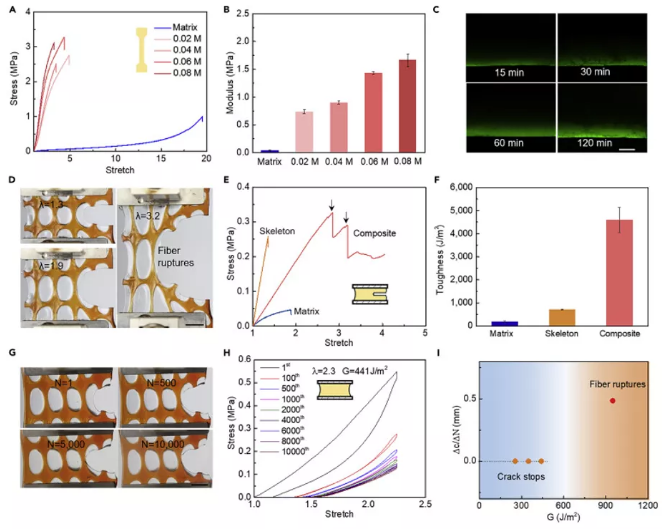
The stereolithography technology can be used to obtain hydrogels with a characteristic size of <100μm. The above-mentioned method for preparing heterogeneous hydrogels can be widely used in various materials. You can also choose poly(N-isopropylacrylamide) (PNIPAm). ), poly(hydroxyethyl methacrylate) (PHEMA) and gelatin as soft hydrogel matrix. PAAm/alginate reinforced by different ions can be used as a raw material for stereolithography to print a rigid hydrogel skeleton. The diversified combination of soft matrix and framework can greatly expand the application range of heterogeneous hydrogels. 【performance】
The mechanical properties of the two hydrogels were measured. The ultimate stretch of the soft hydrogel was about 20 and the modulus was 0.042 MPa; the ultimate stretch of the hard hydrogel was about 4, and the modulus was about 1 MPa. The properties of complex and crosslinked hydrogels are widely adjustable. A longer soaking time and a larger weight ratio of AA to AAm are conducive to the improvement of modulus. The polymer network of soft hydrogel and hard hydrogel will form a topologically entangled structure, and the diffusion of the soft hydrogel precursor to the hard hydrogel can be observed under a confocal microscope. The mesh size of the hydrogel polymer network is about 10 nm, the diffusion length of the precursor increases with time, and the depth can reach 100 μm. The high depth diffusion ensures the topological entanglement between the two constituent hydrogels. The toughness of heterogeneous hydrogel is 4,599±545 J/m 2, which is much higher than the toughness of hard hydrogel (710±19J/m 2) and soft hydrogel (186±41J/m 2) . The modulus of the heterogeneous hydrogel is about 0.18 MPa, which is between the hard matrix and the soft matrix. The adhesion between the composite components helps to achieve high fatigue resistance. For heterogeneous hydrogels with weak adhesion, even if the skeleton remains intact, the cracks will spread in the matrix.
[Application] Use the clinical image data of the human heart valve to build a CAD model, and then convert the CAD model into a printable digital model to print a homogeneous hydrogel structure. However, for the heterogeneous hydrogel structure, the CAD model needs to be modified to a hollow model, the printed hollow structure is immersed in the FeCl 3 solution, and then the soft hydrogel matrix is cast to obtain the heterogeneous hydrogel. In this paper, the anti-fatigue properties of the two hydrogels are evaluated through the extracorporeal hemodynamic test system (Figure E below). This "heart valve" can maintain a continuous one-way flow of liquid. The homogeneous hydrogel fails after 560 cycles. The heterogeneous hydrogel is still intact after 10,000 cycles, showing excellent fatigue resistance. In the composite hydrogel, the skeleton provides the rigidity needed to regulate the water flow, and the soft gel matrix is soft enough to disperse the stress in the skeleton on the one hand, and hard enough to withstand the pressure of the water flow on the other hand. [Conclusion] When preparing objects with open shapes, the combined use of stereolithography and casting technology has great advantages. This method can be used to make complex shapes based on other types of hydrogels. Human heart valves require high mechanical and biological requirements. The heterogeneous hydrogel in the article may not meet the requirements of the in vivo microenvironment, and stress attenuation occurs under cyclic loading (the carboxyl-Fe3+ complex in PAAm-PAA hydrogel) It is caused by breakage of position bonds), so it is still necessary to study a hard hydrogel that combines low hysteresis and high modulus to better simulate heart valves. The synthetic artificial heart is still obstructive and long, but the method mentioned in the article solves the problem that the previous hydrogel cannot achieve complex shapes and high fatigue resistance. It is expected to produce mechanical functions and biological phases by adjusting raw materials and manufacturing processes. Capacitive artificial heart valve.
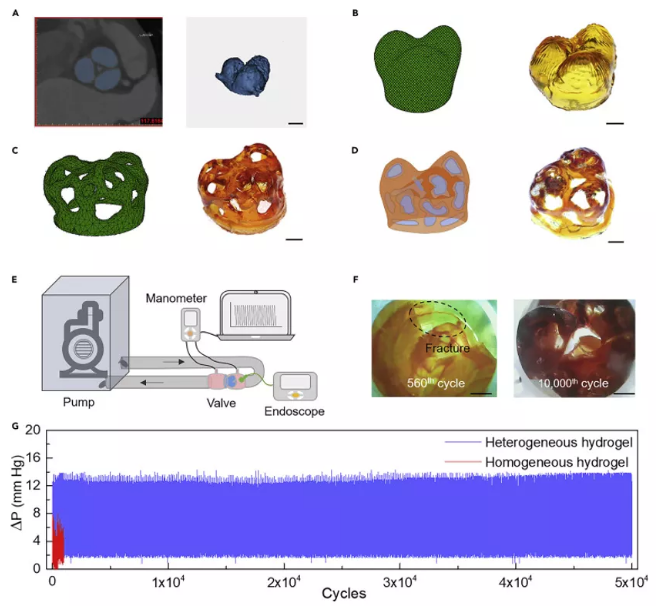
Article source: https://doi.org/10.1016/j.matt.2021.03.011 Yang et al., Matter4, 1–12 June 2, 2021
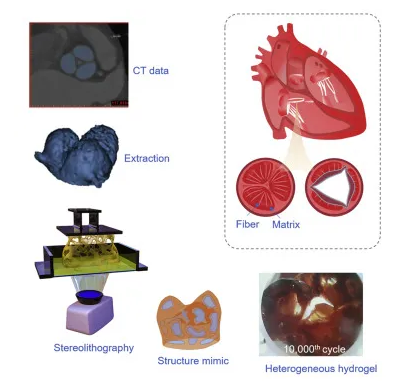
[Structural design and preparation of hydrogels] In order to obtain high fatigue resistance, the two hydrogels should have large modulus contrast and strong adhesion at the interface. The carboxyl-Fe 3+ complex-reinforced polyacrylamide-polyacrylic acid (PAAm-PAA) hydrogel is used as the backbone, and its modulus is about 1 MPa. In addition, PAAm hydrogel is selected as the soft matrix, with a modulus of 0.01-0.1 MPa. As shown in the figure below, a variety of different shapes of hydrogel skeletons can be manufactured by stereolithography.
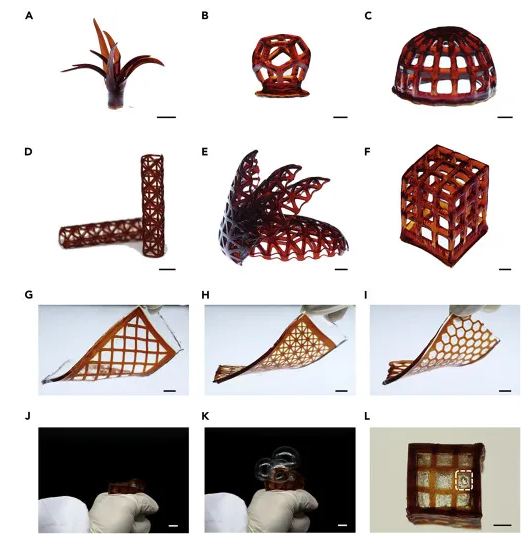
Place the completed skeleton in a mold, and inject the PAAm precursor to polymerize the soft hydrogel matrix. The hydrogel precursor easily migrates into the polymer network of the backbone, so the soft matrix and the polymer network of the backbone will form a topologically entangled structure. A thin layer of soft matrix can be poured on the surface of the hollow cube to obtain the framework-matrix composite material. When the cube is extruded, it will bulge a little (J), suddenly expand (K), or even randomly due to the presence of air. The position is broken (L), which shows that the airtightness of the composite cube is very good, as shown in the figure below.
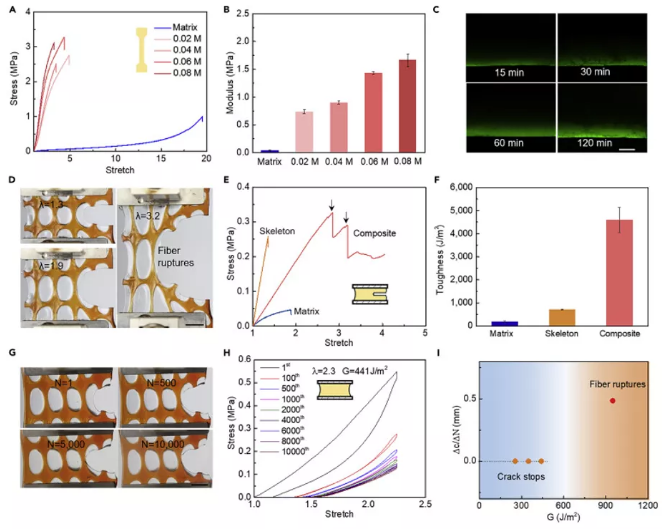
The stereolithography technology can be used to obtain hydrogels with a characteristic size of <100μm. The above-mentioned method for preparing heterogeneous hydrogels can be widely used in various materials. You can also choose poly(N-isopropylacrylamide) (PNIPAm). ), poly(hydroxyethyl methacrylate) (PHEMA) and gelatin as soft hydrogel matrix. PAAm/alginate reinforced by different ions can be used as a raw material for stereolithography to print a rigid hydrogel skeleton. The diversified combination of soft matrix and framework can greatly expand the application range of heterogeneous hydrogels. 【performance】
The mechanical properties of the two hydrogels were measured. The ultimate stretch of the soft hydrogel was about 20 and the modulus was 0.042 MPa; the ultimate stretch of the hard hydrogel was about 4, and the modulus was about 1 MPa. The properties of complex and crosslinked hydrogels are widely adjustable. A longer soaking time and a larger weight ratio of AA to AAm are conducive to the improvement of modulus. The polymer network of soft hydrogel and hard hydrogel will form a topologically entangled structure, and the diffusion of the soft hydrogel precursor to the hard hydrogel can be observed under a confocal microscope. The mesh size of the hydrogel polymer network is about 10 nm, the diffusion length of the precursor increases with time, and the depth can reach 100 μm. The high depth diffusion ensures the topological entanglement between the two constituent hydrogels. The toughness of heterogeneous hydrogel is 4,599±545 J/m 2, which is much higher than the toughness of hard hydrogel (710±19J/m 2) and soft hydrogel (186±41J/m 2) . The modulus of the heterogeneous hydrogel is about 0.18 MPa, which is between the hard matrix and the soft matrix. The adhesion between the composite components helps to achieve high fatigue resistance. For heterogeneous hydrogels with weak adhesion, even if the skeleton remains intact, the cracks will spread in the matrix.
[Application] Use the clinical image data of the human heart valve to build a CAD model, and then convert the CAD model into a printable digital model to print a homogeneous hydrogel structure. However, for the heterogeneous hydrogel structure, the CAD model needs to be modified to a hollow model, the printed hollow structure is immersed in the FeCl 3 solution, and then the soft hydrogel matrix is cast to obtain the heterogeneous hydrogel. In this paper, the anti-fatigue properties of the two hydrogels are evaluated through the extracorporeal hemodynamic test system (Figure E below). This "heart valve" can maintain a continuous one-way flow of liquid. The homogeneous hydrogel fails after 560 cycles. The heterogeneous hydrogel is still intact after 10,000 cycles, showing excellent fatigue resistance. In the composite hydrogel, the skeleton provides the rigidity needed to regulate the water flow, and the soft gel matrix is soft enough to disperse the stress in the skeleton on the one hand, and hard enough to withstand the pressure of the water flow on the other hand. [Conclusion] When preparing objects with open shapes, the combined use of stereolithography and casting technology has great advantages. This method can be used to make complex shapes based on other types of hydrogels. Human heart valves require high mechanical and biological requirements. The heterogeneous hydrogel in the article may not meet the requirements of the in vivo microenvironment, and stress attenuation occurs under cyclic loading (the carboxyl-Fe3+ complex in PAAm-PAA hydrogel) It is caused by breakage of position bonds), so it is still necessary to study a hard hydrogel that combines low hysteresis and high modulus to better simulate heart valves. The synthetic artificial heart is still obstructive and long, but the method mentioned in the article solves the problem that the previous hydrogel cannot achieve complex shapes and high fatigue resistance. It is expected to produce mechanical functions and biological phases by adjusting raw materials and manufacturing processes. Capacitive artificial heart valve.
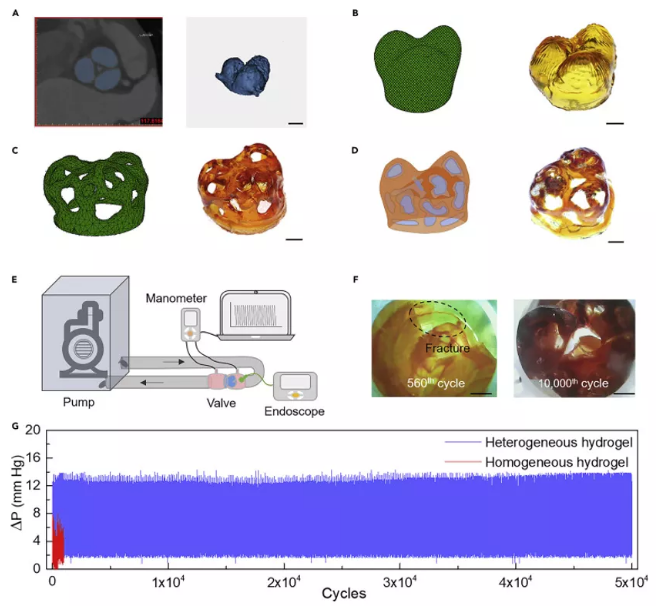
Article source: https://doi.org/10.1016/j.matt.2021.03.011 Yang et al., Matter4, 1–12 June 2, 2021
- Previous: The shot is 2 Nature N
- Next: A Rising 2D Star: Nove