Recommended by Nature! Inspired by lobster, MIT Zhao Xuanhe team developed a highly anti-fatigue nanofiber hydrogel
QQ Academic Group: 1092348845
Detailed
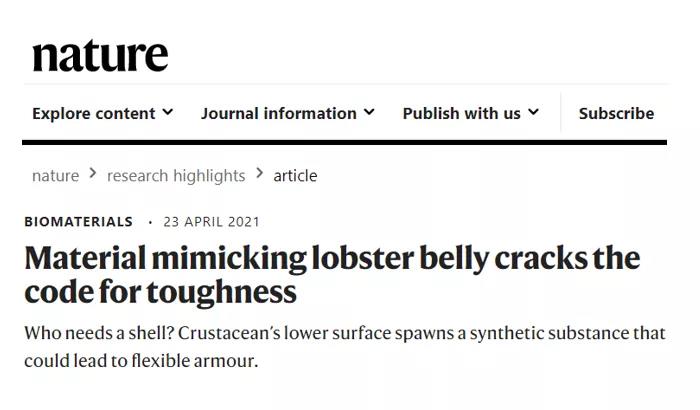
The abdomen of the lobster is covered with a translucent film, which is both elastic and surprisingly tough. This underwater armor is made from the hardest hydrogel known in nature, and this hydrogel happens to be highly flexible. When the lobster is struggling on the bottom of the sea, this combination of strength and softness helps to protect it while swimming forward.
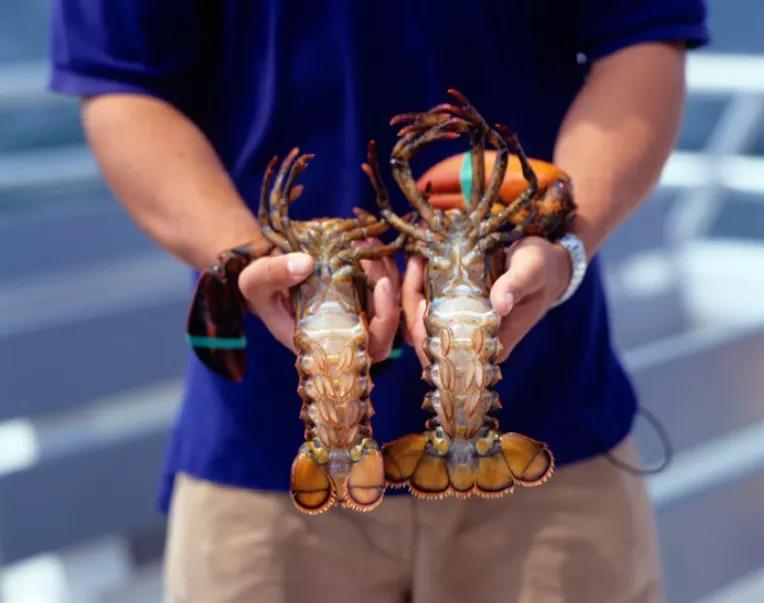
The Zhao Xuanhe team of the Massachusetts Institute of Technology imitated the structure of the lobster abdomen to create nanofiber hydrogels. A series of tensile and impact tests show that this synthetic material has significant "fatigue resistance" and can withstand repeated stretching and pulling without tearing. Nanofiber hydrogel materials are expected to be used to manufacture alternative tissues with elasticity and strength, such as artificial tendons and ligaments. The teams research results were published in the "Matter" magazine under the title "Strong fatigue-resistant nanofibrous hydrogels inspired by lobster underbelly".
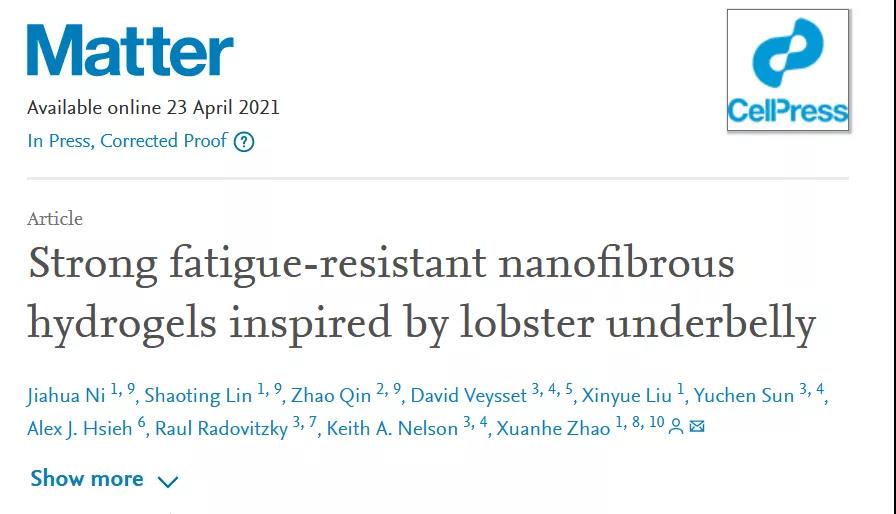
[Nano fiber hydrogel design inspired by lobster abdomen]
Nanofiber hydrogels are commonly found in animals and plants. They have the advantages of high porosity, high water content and biocompatibility. They can be used in tissue regeneration, ionic skin, hemostatic dressings, cartilage repair, textile sensors, printable Flexible implanted electrodes, tissue adhesives, and small bio-robots. Electrospinning is one of the most extensive methods for preparing nanofiber hydrogels, because electrospinning can obtain relatively uniform fiber diameter and adjustable fiber structure. The existing electrospun nanofiber hydrogels are usually fragile because of the low strength and weak interface of nanofibers. In particular, the presence of water will gradually expand the nanofibers and attack the interface between the nanofibers, thereby forming a fragile nanofiber network. Researchers have improved the strength and toughness of nanofiber hydrogels by introducing strong chemical crosslinks. However, this reinforced nanofiber hydrogel is still prone to fatigue failure under multiple cycles. Studies have shown that the soft membrane of the lower abdomen of the lobster is a natural hydrogel with extremely high fracture toughness (24.98 MJ/m3) and tensile strength (23.36 MPa) under cyclic loading. From the perspective of bionics, Professor Zhao Xuanhe imitated the material and structure of the lobster abdomen, designed and manufactured nanofiber hydrogel, which achieved a tensile strength of 8.4 MPa and fatigue resistance of 770 J/m2. In the case of a tensile stress of 1 MPa, after a long time cycle, it can bear 3000 times its own weight in the dry state, and has a superior penetration power of 40 kJ/kg in the hydrated state, and has superior impact resistance Performance is comparable to polyethylene.
The author chooses polyvinyl alcohol (PVA) as the model material system of nanofiber hydrogels. The crystallinity of nanofibers is adjustable, and the interface between nanofibers is adjustable. The author further quantified the contribution of the interface strength between nanofibers to the overall strength of the nanofiber network. In addition, the author established a theoretical model to explain the relationship between the nanofiber structure and the fatigue threshold of the fiber network.
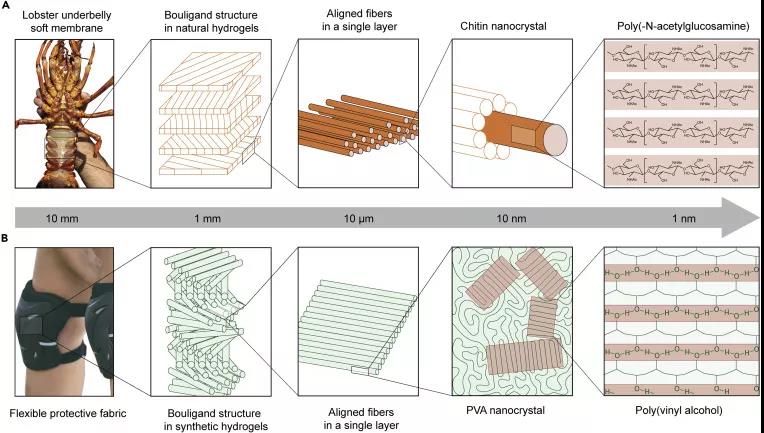
Figure 1 Strong anti-fatigue nanofiber hydrogel inspired by "lobster belly"
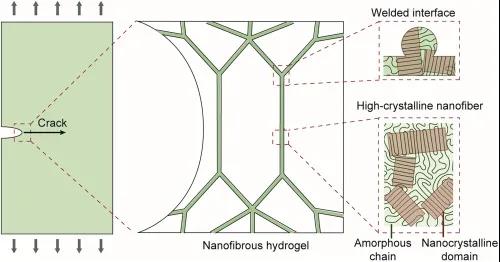
Figure 2 Design principle of high-strength and anti-fatigue nanofiber hydrogels: Strong anti-fatigue nanofiber hydrogels require the synergy between nanofibers and high-crystalline nanofibers. This welding interface can resist fatigue and reduce crack propagation .
[Structure and mechanical properties of nanofiber hydrogel]
The author prepared nanofiber hydrogels based on the sequence of electrospinning, welding and dry annealing, and characterized them by scanning electron microscope (SEM) and scanning calorimetry (DSC). The author found that with the prolongation of water vapor exposure, the strength of the welded nanofiber network increased, but excessive exposure to water vapor would completely dissolve the PVA nanofibers, resulting in damage to the nanofiber structure. Therefore, a moderate amount of water was set for 6 minutes. The vapor exposure time is to ensure a strong interface between the nanofibers while maintaining the PVA structure of the nanofibers.
The authors characterized the mechanical properties of various nanofiber hydrogels under different conditions. As shown in Figure 3, the nanofiber hydrogel with low crystallinity and weak interface can not withstand any mechanical load when it is immersed in water due to its decomposition into isolated nanofibers. In contrast, the strength of nanofiber hydrogel with low crystallinity and strong interface is 4 MPa, but due to brittle fracture caused by the highly cross-linked polymer of glutaraldehyde, the final tensile strain is only 1.2. The tensile strain of nanofiber hydrogel with high crystallinity and weak interface can reach 2.25, but the strength is only 1.4 MPa. In contrast, nanofiber hydrogels with high crystallinity and strong interface have high strength (3.5 MPa) and high tensile properties (tensile strain up to 3.4). The author further characterized the fatigue performance of different nanofiber hydrogels under dynamic cyclic loading. As shown in Figure 3K, the fatigue threshold of the nanofiber hydrogel with high crystallinity and strong interface reaches 600 J/m2, and the fatigue threshold of the nanofiber hydrogel with high crystallinity and weak interface is 320 J/m2.
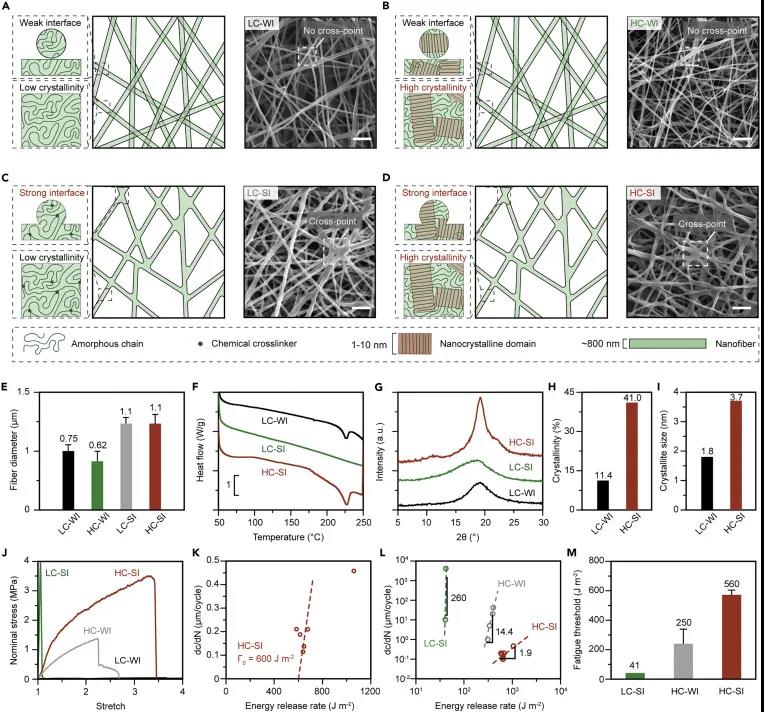
Figure 3 Structure and mechanical properties of nanofiber hydrogel
The author further developed a nanofiber network model to simulate the mechanical response of the nanofiber network under tensile load. As the interface strength decreases, the fiber network becomes weaker and the stretchability becomes worse. The simulation results show that the mechanical response of the fiber network is mainly affected by the strength of the interface, rather than the extensibility of the interface. The fatigue crack growth in the nanofiber network is similar to the fatigue crack growth in the polymer network, which can be explained by the Lake-Thomas model, as shown in the in-situ confocal laser scanning microscope images and images of Figures 5C and 5D.
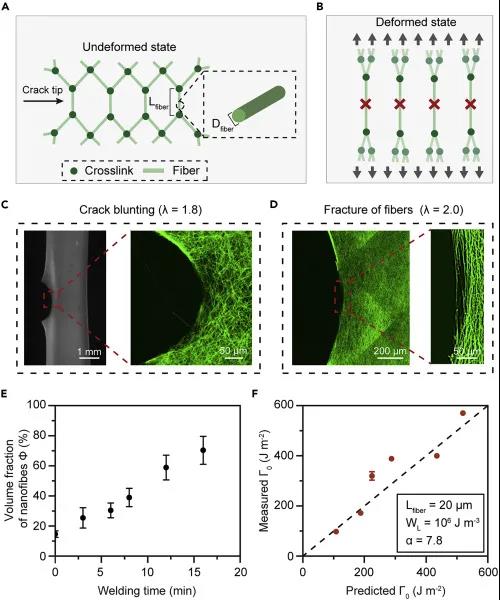
Figure 5 Theoretical model for predicting the fatigue threshold of nanofibrous hydrogel networks
In summary, Professor Zhao Xuanhes team has provided a general strategy for designing anti-fatigue nanofiber hydrogels, which is achieved through the strong combination of nanofibers and nanocrystalline domains. Studies have shown that the synergistic effect of introducing nanocrystal domains into nanofibers and the combination of adjacent nanofibers can significantly increase the fatigue threshold of nanofiber hydrogels from 41 J/m2 to 600 J/m2. Inspired by the lobster abdomen, this research has opened up a path for various emerging applications of next-generation nanofiber hydrogels, including artificial tissue replacement, lightweight physical protection, textile electronics, smart clothing, and tissue engineering scaffolds.
Full text link:
https://www.sciencedirect.com/science/article/pii/S2590238521001612
- Previous: Sci. Adv. by Gong Jian
- Next: A Rising 2D Star: Nove