Ultrason. Sonochem.|Ultrasonic-assisted synthesis enhances energy storage performance of MXene
QQ Academic Group: 1092348845
Detailed
North Konami can provide Ti3C2Tx MXene (customizable)
Research abstract

Ti3C2Tx MXenes, usually obtained by etching the main group elements in their corresponding transition metal carbide MAX phases, exhibit excellent electrochemical performance in energy storage applications thanks to unique physicochemical properties. However, the low efficiency of main group element removal (so-called chemical etching) severely limits the application prospects of MXene and MXene-related materials. In view of this, the research team of Professor Zhang Wu of Shenyang University of Technology published the latest research results in "Ultrasonic Sonochemistry", and reported an ultrasonic-assisted method to synthesize Ti3C2Tx MXene using Ti3AlC2 as a precursor. The experimental data show that the chemical etching efficiency of Ti3AlC2 is greatly improved under ultrasonic conditions, and the etching time in dilute hydrochloric acid solution is shortened from 24 hours to 8 hours. In particular, high etching efficiency can be achieved in a 2% hydrofluoric acid solution under the assistance of ultrasound, and the concentration of 2% is lower than the etching environment that has been reported so far. The specific capacity of the samples obtained by 8 hours of ultrasonication can reach 155 F/g, which is much larger than the capacitance value of the samples prepared without ultrasonic assistance under the same conditions. In addition, after 20,000 charge-discharge cycles, the ultrasonic-assisted sample can achieve a capacitance retention rate of 97.5%, showing outstanding energy storage stability compared with previous reports. At the same time, this ultrasonic-assisted process can more efficiently remove the AlF3 impurities generated on the surface of the etchant, and the acoustic cavitation effect generated during the ultrasonic treatment can destroy the hydrogen bonds between the functional groups of two adjacent layers.
Graphical guide
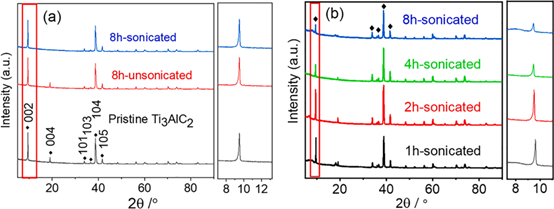
Figure 1. XRD patterns of different stages of the ultrasonic etching process of Ti3AlC2.
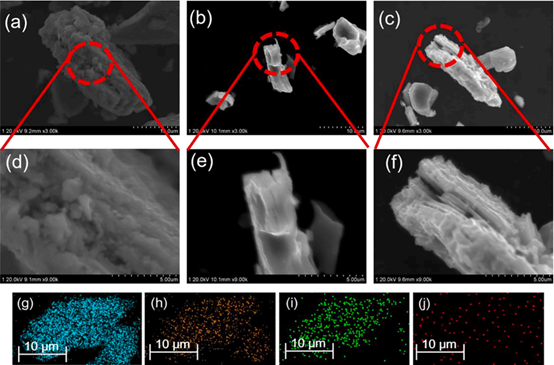
Figure 2. SEM images and elemental mapping of Ti3C2Tx MXene under different ultrasound-assisted conditions.
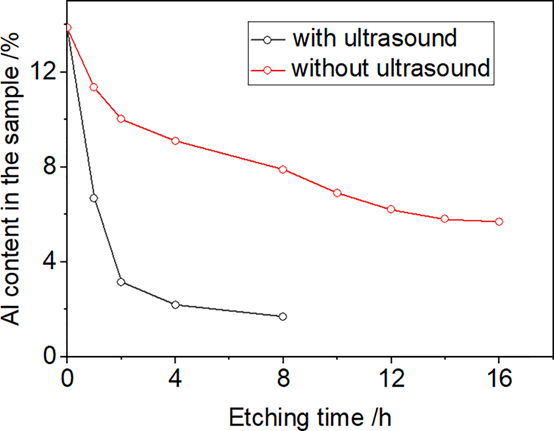
Figure 3. The relationship between the Al content after etching and the ultrasonic-assisted etching time.
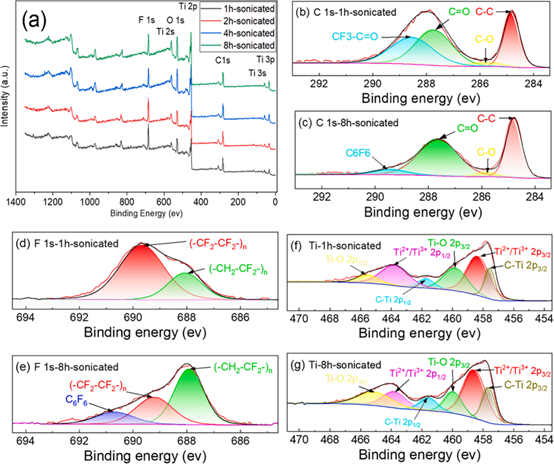
Figure 4. XPS full-spectrum and high-resolution spectra at different ultrasound-assisted etching times.
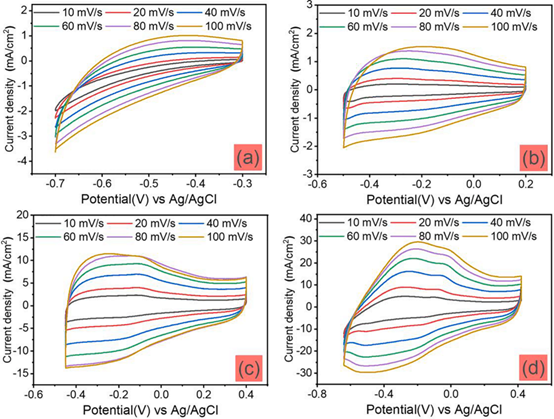
Figure 5. CV cyclic voltammetry curves of samples prepared with different ultrasonic-assisted etching times at different scan rates.
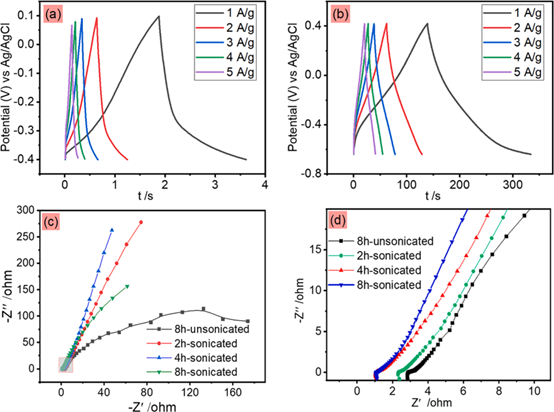
Figure 6. Galvanostatic charge-discharge curves and EIS impedance curves of samples prepared with different ultrasonic-assisted etching times.
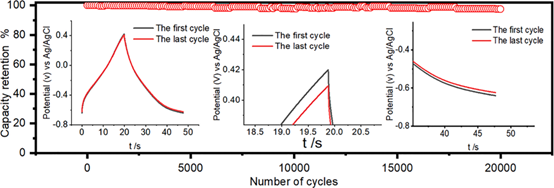
Figure 7. Cycling stability of the 8-hour ultrasound-assisted prepared samples at a current density of 5 A/g.
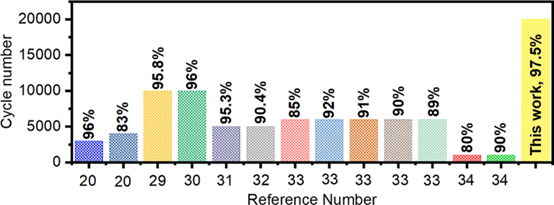
Figure 8. Capacitance retention of the samples prepared by 8 hours of ultrasonic-assisted etching compared with the samples reported in the previous literature.
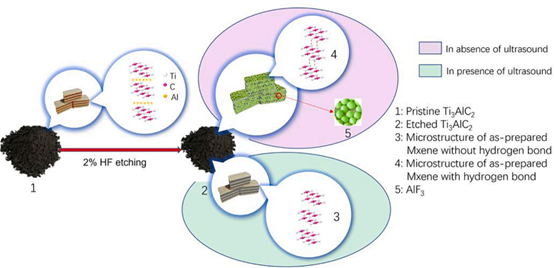
Figure 9. The technical roadmap for the preparation of MXene by ultrasonic-assisted etching.
Summarize
Summarize
picture
The Ti3C2Tx prepared by the ultrasonic-assisted method proposed in this work exhibited an obvious accordion structure on the microscopic scale. The XRD results show that the (002) crystal face of the etched samples has a lower diffraction peak angle, which is mainly due to the expansion of the interlayer space. Under the ultrasonic condition, the shift of the peak position is more obvious. After ultrasonic etching, only 1.63 wt% of Al remained in the obtained samples, while the proportion of Al residues was as high as 7.88 wt% under non-ultrasonic conditions, indicating that this ultrasonic-assisted method can efficiently remove the precursor MAX phase. main group element. At the same time, under the same experimental conditions, the capacitance value of the samples prepared by the ultrasonic-assisted method was 45 times higher than that of the samples prepared under the non-ultrasonic conditions.
picture
Literature link
https://doi.org/10.1016/j.ultsonch.2022.106024
For the original text, please click the lower left corner of the tweet to read the original text
Research abstract

Ti3C2Tx MXenes, usually obtained by etching the main group elements in their corresponding transition metal carbide MAX phases, exhibit excellent electrochemical performance in energy storage applications thanks to unique physicochemical properties. However, the low efficiency of main group element removal (so-called chemical etching) severely limits the application prospects of MXene and MXene-related materials. In view of this, the research team of Professor Zhang Wu of Shenyang University of Technology published the latest research results in "Ultrasonic Sonochemistry", and reported an ultrasonic-assisted method to synthesize Ti3C2Tx MXene using Ti3AlC2 as a precursor. The experimental data show that the chemical etching efficiency of Ti3AlC2 is greatly improved under ultrasonic conditions, and the etching time in dilute hydrochloric acid solution is shortened from 24 hours to 8 hours. In particular, high etching efficiency can be achieved in a 2% hydrofluoric acid solution under the assistance of ultrasound, and the concentration of 2% is lower than the etching environment that has been reported so far. The specific capacity of the samples obtained by 8 hours of ultrasonication can reach 155 F/g, which is much larger than the capacitance value of the samples prepared without ultrasonic assistance under the same conditions. In addition, after 20,000 charge-discharge cycles, the ultrasonic-assisted sample can achieve a capacitance retention rate of 97.5%, showing outstanding energy storage stability compared with previous reports. At the same time, this ultrasonic-assisted process can more efficiently remove the AlF3 impurities generated on the surface of the etchant, and the acoustic cavitation effect generated during the ultrasonic treatment can destroy the hydrogen bonds between the functional groups of two adjacent layers.
Graphical guide
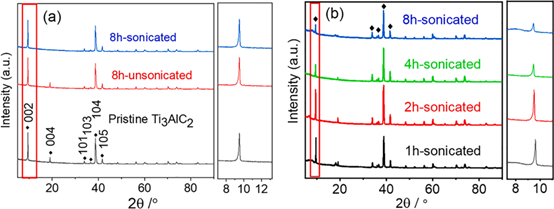
Figure 1. XRD patterns of different stages of the ultrasonic etching process of Ti3AlC2.
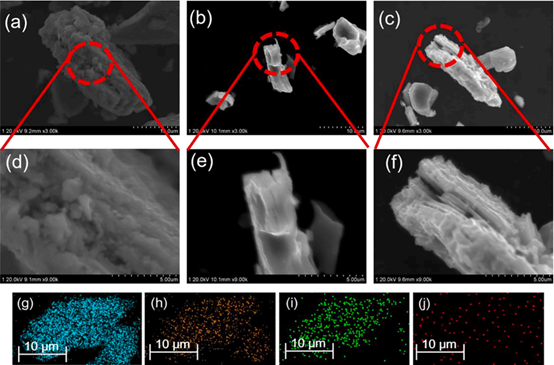
Figure 2. SEM images and elemental mapping of Ti3C2Tx MXene under different ultrasound-assisted conditions.
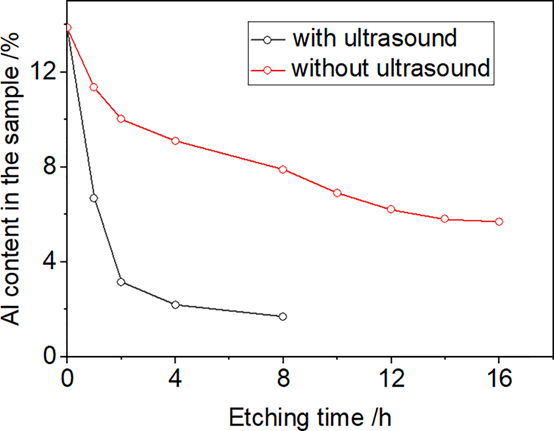
Figure 3. The relationship between the Al content after etching and the ultrasonic-assisted etching time.
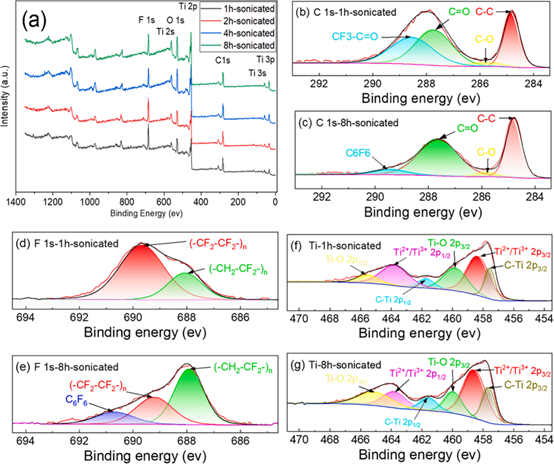
Figure 4. XPS full-spectrum and high-resolution spectra at different ultrasound-assisted etching times.
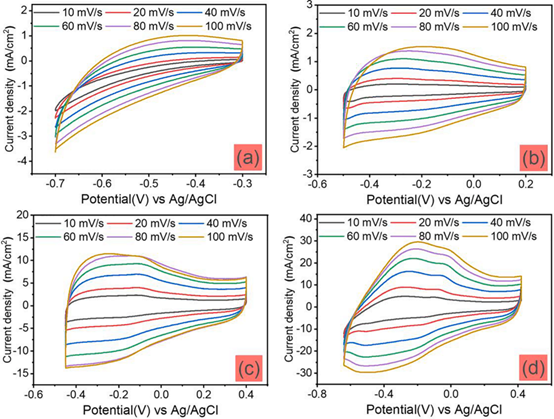
Figure 5. CV cyclic voltammetry curves of samples prepared with different ultrasonic-assisted etching times at different scan rates.
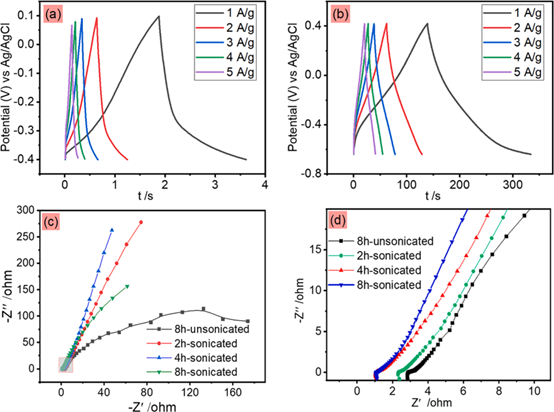
Figure 6. Galvanostatic charge-discharge curves and EIS impedance curves of samples prepared with different ultrasonic-assisted etching times.
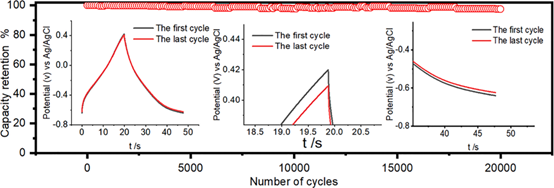
Figure 7. Cycling stability of the 8-hour ultrasound-assisted prepared samples at a current density of 5 A/g.
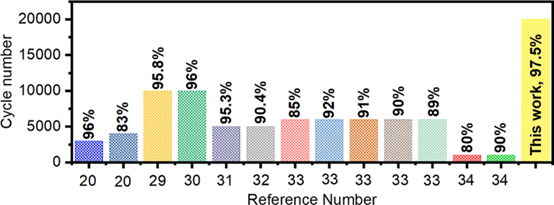
Figure 8. Capacitance retention of the samples prepared by 8 hours of ultrasonic-assisted etching compared with the samples reported in the previous literature.
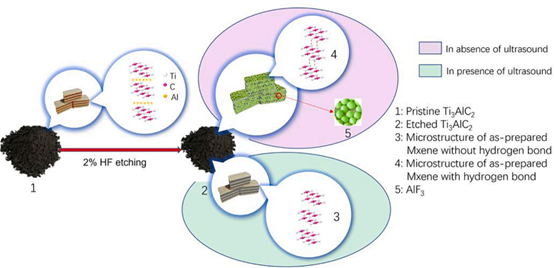
Figure 9. The technical roadmap for the preparation of MXene by ultrasonic-assisted etching.
Summarize
Summarize
picture
The Ti3C2Tx prepared by the ultrasonic-assisted method proposed in this work exhibited an obvious accordion structure on the microscopic scale. The XRD results show that the (002) crystal face of the etched samples has a lower diffraction peak angle, which is mainly due to the expansion of the interlayer space. Under the ultrasonic condition, the shift of the peak position is more obvious. After ultrasonic etching, only 1.63 wt% of Al remained in the obtained samples, while the proportion of Al residues was as high as 7.88 wt% under non-ultrasonic conditions, indicating that this ultrasonic-assisted method can efficiently remove the precursor MAX phase. main group element. At the same time, under the same experimental conditions, the capacitance value of the samples prepared by the ultrasonic-assisted method was 45 times higher than that of the samples prepared under the non-ultrasonic conditions.
picture
Literature link
https://doi.org/10.1016/j.ultsonch.2022.106024
For the original text, please click the lower left corner of the tweet to read the original text
- Previous: MXene-based biomimetic
- Next: MXene breakthrough: Na