3D printed custom MXene architecture
QQ Academic Group: 1092348845
Detailed
Formulating 3D-printable MXene inks and integrating them into custom 3D device architectures will provide a high degree of architectural control, scalability, and cost effectiveness. However, this will require that inks with a single or few layers of MXene must achieve the rheological properties required for 3D printing.
The 3D printing architecture consisting of MXene is particularly attractive for energy storage applications such as rechargeable lithium-ion and sodium-ion batteries, lithium-sulfur batteries, and supercapacitors. They can also be used for other applications such as energy conversion, photocatalytic fuel production or electromagnetic shielding.
For the first time, researchers at the University of Manchester have demonstrated the possibility of printing 3D independent MXene objects. They developed a 3D printing ink consisting of only a few large layers of MXene flakes and water as a solvent, without using additives to control the rheology of the ink.
The team published their findings in advanced materials ("3D printing of standalone MXene architecture for supercapacitors without current collectors").
The ability to print a custom MXene architecture in three dimensions provides new opportunities for achieving the high-performance multi-scale and multi-dimensional equipment required for many different energy, catalytic and transportation applications.
Dr. Suelen Barg said, "We have formulated the most researched MXene material 2D Ti 3 C 2 T x with water-based inks. It has ideal viscoelasticity and can be used for extrusion-based construction of freestanding, high specific surface areas of different sizes and shapes 3D printing. "The structural materials lecturer in the Materials Department told Nanowerk. "The inks we have developed translate the properties of 2D materials into 3D, resulting in a significantly higher specific surface area of the architecture compared to other methods."
Multiscale architecture for 3D printing after freeze drying. a, b) SEM and optical photographs (inset) of independent Ti 3 C 2 T x microlattices (a) and hollow rectangular prisms (b) printed through 330 and 250 μm nozzles, respectively. (Reprinted with permission from Wiley-VCH Verlag) (click on the image to enlarge)
In the first study of MXene‘s 3D printability, the team demonstrated that by formulating an ink consisting of a large size (average lateral dimension of 8 μm) and several thin layers (thickness of 1-3 nm) of MXene flakes and water Its rheological properties can be adjusted to allow them to be extruded through micron-sized nozzles. In addition, the extruded filament can maintain its shape in excess of 20 printed layers.
After printing, the team freeze-dried the wet 3D structure to protect the internal integrity and external shape of the structure with low shrinkage. The result is a well-defined free-standing MXene architecture without any further heat or chemical treatment.
"In addition to various 3D architectures such as microlattices and hollow rectangular prisms, we also use Ti 3 C 2 T x as electrode materials and current collectors to further apply inks to the direct interdigitated supercapacitors with solid electrolytes. On printing. "" This eliminates the need to use precious metals or other metallic materials as current collectors in 3D printed electrode designs. "
An electrode with an active material load of about 8.5 mg cm -2 exhibits an area capacitance of 2.1 F cm -2, high power and energy density, and a capacitance retention rate of more than 90% in 10,000 cycles.
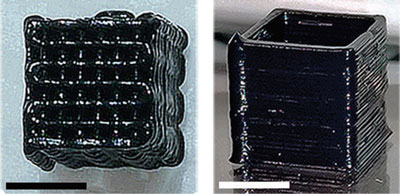
3D printed illustration of the MXene architecture with 25 printed layers per layer. Left: 3D printed microlattice. Right: rectangular hollow prism. Printed through 330 μm and 250 μm nozzles, respectively. Scale bar: 3 mm. (Reprinted with permission from Wiley-VCH Verlag)
"These results are the highest in the literature and confirm that our synthesis and processing routes can translate the performance of 2D materials to assembled 3D devices," Wangji Yang (currently a PhD student and first author of the Barg Group) ) Pointed out.
In the next step, the team will optimize its MXene ink formulations and additive manufacturing protocols, manufacture custom energy storage devices in asymmetric configurations, and use multi-material printing and alternative electrolytes to overcome voltage window limitations and further increase energy in energy storage devices. density.
They are also exploring their 3D printable inks in other applications that can benefit from the MXene tunable 3D architecture, such as electromagnetic shielding and catalysis.
Barg concluded: "The 3D printability of MXenes encourages us to explore the development of inks that combine other functional materials." "Special challenges and potential research directions include controlling the oxidation of MXene inside water-based inks and better controlling and understanding of water insertion. The role of layers in the formation and properties of MXene inks and their relationship to printability. "
Source: nanowerk
- Previous: Mxene: A New Kind of N
- Next: MXene breakthrough: Na