Direct laser writing of graphene on Kevlar fibers makes protective clothing
QQ Academic Group: 1092348845
Detailed
(Nanowerk Spotlight) Kevlar fiber is a well-known high-strength polymer. Due to its excellent mechanical properties, various important safety applications have been discovered, from textiles (such as bulletproof vests or firefighters‘ protective clothing) to Tough composite materials (such as automotive armor panels).
Multifunctional preparation for the next generation of protective clothing, "smart". Not only do these materials protect the human body from harm, they also have intelligent functions such as monitoring physiological signals and detecting potential hazards such as gases, pathogens or radiation.
In order to make "smart" clothing, functional materials must be combined with fibers or textiles, usually in the form of nanofinishing, where a series of nanomaterials (such as carbon nanotubes, graphene, or silver nanowires) can be deposited onto On textiles.
"Generally speaking, these methods all require multi-step routes and time-consuming precursor preparation processes," explains Yingying Zhang, associate professor of chemistry and center at Tsinghua University in Beijing, Department of Nano and Micromechanics (CNMM), explained Nanowerk. "Therefore, it is still challenging to make smart protective clothing through simple methods, especially those with arbitrary patterns or custom design features."
Back in 2014, Rice University researchers used a computer-controlled laser to burn a cheap polymer to create a flexible, patterned multilayer graphene sheet, a technique called laser Induced Graphene (LIG). This high-yield, low-cost graphene synthesis process can work in air at room temperature, does not require a hot furnace and a controlled environment, and makes graphene suitable for electronics or energy storage.
Zhang said: "This laser writing method for preparing graphene on polyimide, wood or paper is simple, efficient and flexible in design." "Based on the fact that there are similar polymer structures in textiles, we assume that we can Applying laser writing technology to polymer textiles makes it easy to make graphene-based textile electronics. "
In a new paper published on ACS Nano ("Janus Graphene / Kevlar Fibers for Laser Writing of Smart Protective Clothing"), Zhang and his team reported the effects of laser-induced graphene on Kevlar fibers. Write directly.
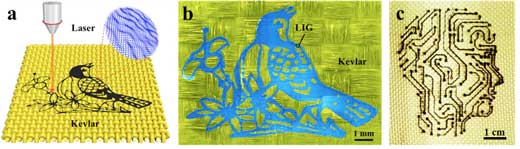
Laser writing writes graphene on Kevlar fabric. (A) Schematic of graphene / Kevlar textiles made by Kevlar. (B) The SEM image of LIG is patterned into the shape of a bird. (C) The digital image of LIG is patterned into the shape of a person‘s side. (Reprinted with permission from the American Chemical Society) (click image to enlarge)
According to the team, Kevlar‘s conversion to graphene can be attributed to the photothermal effect caused by CO 2 laser irradiation. In particular, this leads to higher local temperatures, leading to the ablation and deagglomeration of Kevlar fibers. The remaining carbon atoms recombine and "recrystallize" into graphene.
What they call Janus graphene / Kevlar fiber textiles-with porous graphene on the front and Kevlar fibers on the back-can be made in air. To prevent graphene from falling off the fabric, the researchers dropped pre-cured Ecoflex on the surface of the processed fabric to form a very thin coating to hold and encapsulate graphene.
Direct writing of graphene from commercial textiles under air conditions is simple, efficient, and flexible in design, opening up a new path for the development of cost-effective and custom-designed textile electronics. For example, it provides a versatile and fast way to make textile electronics, such as flexible supercapacitors and sensors for monitoring human physiological conditions in the field.
Zhang pointed out: "Before doing this work, we didn‘t know that textiles could be transformed into graphene under air conditions." "Our research team focuses on the design and manufacture of new flexible and wearable materials and electronics. In recent years , We are very interested in developing fibers and textile electronic materials made of nano-carbon and silk materials. Our goal is to develop ergonomically correct and excellent performance-this encourages us in Kev Experiments on the laser writing process on Lal. "
Based on this technology, it becomes feasible to prepare various types of flexible electronic devices on different commercial textiles such as silk and cotton. This will make efficient, customized and versatile textile electronics possible.
Direct writing of graphene from commercial textiles with lasers under air conditions also provides a versatile and fast way to make textile electronics such as flexible supercapacitors and sensors.
With the popularity of emerging technologies such as biotechnology, virtual reality and artificial intelligence, the demand for wearable devices is surging. They will change the way we communicate, monitor physiological functions and environmental data, and manage medicine.
Zhang concluded, "Future wearable electronic devices must be ergonomic, biologically safe, and even implantable." "Researchers active in this field need to further explore how to integrate individual electronic devices (such as Sensors, displays, batteries, wireless transmitters, etc.) into a complete flexible system and eventually integrate it with clothing and even medical implants. These ambitious goals require researchers and engineers from different backgrounds to work together on material preparation , Energy equipment, electronics design and manufacturing, data processing, packaging technology, medical technology and other aspects. "
Source: nanowerk
Multifunctional preparation for the next generation of protective clothing, "smart". Not only do these materials protect the human body from harm, they also have intelligent functions such as monitoring physiological signals and detecting potential hazards such as gases, pathogens or radiation.
In order to make "smart" clothing, functional materials must be combined with fibers or textiles, usually in the form of nanofinishing, where a series of nanomaterials (such as carbon nanotubes, graphene, or silver nanowires) can be deposited onto On textiles.
"Generally speaking, these methods all require multi-step routes and time-consuming precursor preparation processes," explains Yingying Zhang, associate professor of chemistry and center at Tsinghua University in Beijing, Department of Nano and Micromechanics (CNMM), explained Nanowerk. "Therefore, it is still challenging to make smart protective clothing through simple methods, especially those with arbitrary patterns or custom design features."
Back in 2014, Rice University researchers used a computer-controlled laser to burn a cheap polymer to create a flexible, patterned multilayer graphene sheet, a technique called laser Induced Graphene (LIG). This high-yield, low-cost graphene synthesis process can work in air at room temperature, does not require a hot furnace and a controlled environment, and makes graphene suitable for electronics or energy storage.
Zhang said: "This laser writing method for preparing graphene on polyimide, wood or paper is simple, efficient and flexible in design." "Based on the fact that there are similar polymer structures in textiles, we assume that we can Applying laser writing technology to polymer textiles makes it easy to make graphene-based textile electronics. "
In a new paper published on ACS Nano ("Janus Graphene / Kevlar Fibers for Laser Writing of Smart Protective Clothing"), Zhang and his team reported the effects of laser-induced graphene on Kevlar fibers. Write directly.
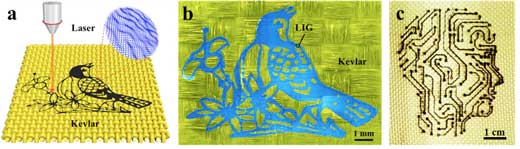
Laser writing writes graphene on Kevlar fabric. (A) Schematic of graphene / Kevlar textiles made by Kevlar. (B) The SEM image of LIG is patterned into the shape of a bird. (C) The digital image of LIG is patterned into the shape of a person‘s side. (Reprinted with permission from the American Chemical Society) (click image to enlarge)
According to the team, Kevlar‘s conversion to graphene can be attributed to the photothermal effect caused by CO 2 laser irradiation. In particular, this leads to higher local temperatures, leading to the ablation and deagglomeration of Kevlar fibers. The remaining carbon atoms recombine and "recrystallize" into graphene.
What they call Janus graphene / Kevlar fiber textiles-with porous graphene on the front and Kevlar fibers on the back-can be made in air. To prevent graphene from falling off the fabric, the researchers dropped pre-cured Ecoflex on the surface of the processed fabric to form a very thin coating to hold and encapsulate graphene.
Direct writing of graphene from commercial textiles under air conditions is simple, efficient, and flexible in design, opening up a new path for the development of cost-effective and custom-designed textile electronics. For example, it provides a versatile and fast way to make textile electronics, such as flexible supercapacitors and sensors for monitoring human physiological conditions in the field.
Zhang pointed out: "Before doing this work, we didn‘t know that textiles could be transformed into graphene under air conditions." "Our research team focuses on the design and manufacture of new flexible and wearable materials and electronics. In recent years , We are very interested in developing fibers and textile electronic materials made of nano-carbon and silk materials. Our goal is to develop ergonomically correct and excellent performance-this encourages us in Kev Experiments on the laser writing process on Lal. "
Based on this technology, it becomes feasible to prepare various types of flexible electronic devices on different commercial textiles such as silk and cotton. This will make efficient, customized and versatile textile electronics possible.
Direct writing of graphene from commercial textiles with lasers under air conditions also provides a versatile and fast way to make textile electronics such as flexible supercapacitors and sensors.
With the popularity of emerging technologies such as biotechnology, virtual reality and artificial intelligence, the demand for wearable devices is surging. They will change the way we communicate, monitor physiological functions and environmental data, and manage medicine.
Zhang concluded, "Future wearable electronic devices must be ergonomic, biologically safe, and even implantable." "Researchers active in this field need to further explore how to integrate individual electronic devices (such as Sensors, displays, batteries, wireless transmitters, etc.) into a complete flexible system and eventually integrate it with clothing and even medical implants. These ambitious goals require researchers and engineers from different backgrounds to work together on material preparation , Energy equipment, electronics design and manufacturing, data processing, packaging technology, medical technology and other aspects. "
Source: nanowerk
- Previous:
- Next: 1