AFM: MXene nanoparticles-nanosheets can be used for high sensitivity and wide range strain sensors
QQ Academic Group: 1092348845
Detailed
【Research Background】
In recent years, stretchable and wearable strain sensors have attracted a lot of attention in academia due to their advantages of portability, foldability, portability, and biocompatibility. Sensitivity (ie, strain factor (GF) and stretchability are two important parameters for evaluating the sensor performance of strain sensors. For small deformations, such as pulse and heartbeat, high sensitivity is required. At the same time, high stretchability is the detection The basis of a lot of body movements caused by joint movements. In general, in order to meet the basic requirements of full-range human motion detection, strain sensors must have a sensing range of more than 50% and a measurement coefficient greater than 100 in the full working range. However, the enhancement of sensitivity and the enhancement of the working range are contradictory, because sensitivity requires significant structural changes to occur at small strains, and stretchability requires the device to maintain the connectivity of the conductive path in the large strain area; therefore, manufacturing the ideal strain Sensors still face huge challenges.
【Achievement Introduction】
In 2019, Associate Researcher Wang Ranran and Researcher Sun Jing from the Shanghai Institute of Ceramics, Chinese Academy of Sciences published an article in the internationally renowned academic journal Advanced Functional Materials: Strain Sensors with a High Sensitivity and a Wide Sensing Range Based on a Ti3C2Tx ( MXene) Nanoparticle–Nanosheet Hybrid Network research paper successfully constructed a unique Ti3C2Tx nanoparticle-nanosheet composite network for strain sensors, which has a high sensitivity (GF>) in the full range (0-53%) 178.4), very low detection limit (0.025%) and good cycle durability (over 5000 cycles). The coordinated movement of Ti3C2Tx nanoparticles and nanosheets is the main reason for their excellent comprehensive performance. Three different sensing stages and constrained micro-crack growth mechanisms were discovered. When stretched, the migration and separation of the nanoparticles cause a large resistance change, and the nanoflakes wrap and bridge the separated nanoparticles, maintaining the connectivity of the conductive path in a large strain area. Different proportions of Ti3C2Tx nanoparticles and nanosheets show the diversity of structure and morphology in the hybrid network, which helps to fully functionalize the microstructure and maximize the synergistic effect. The Ti3C2Tx hybrid network shows quite high sensitivity to sensors based on a single nanoparticle or flake, but its working range has been expanded by 7-10 times.
In addition, demonstrations of human activity detection from precise speech recognition to violent human movements have confirmed the superiority of hybrid networks.
【Graphic introduction】
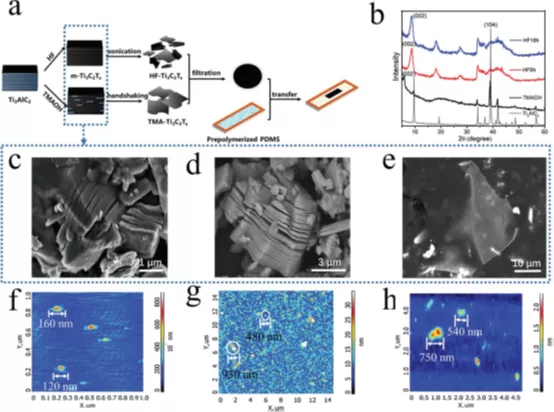
Figure 1. Ti3C2Tx synthesis and characterization.
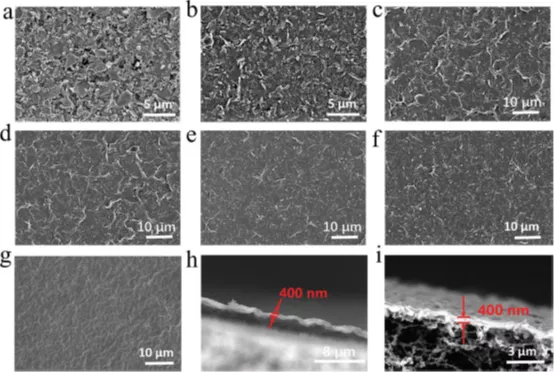
Figure 2. SEM image of Ti3C2Tx conductive film.
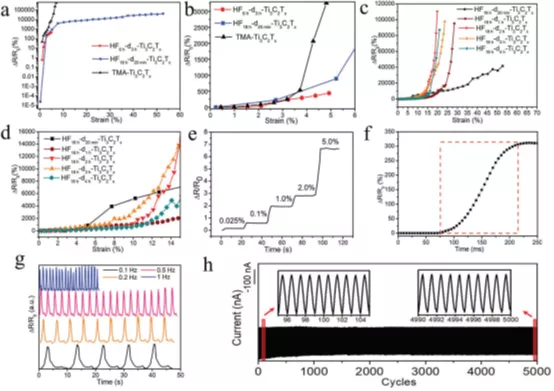
Figure 3. Strain sensing characteristics of a strain sensor based on Ti3C2Tx.
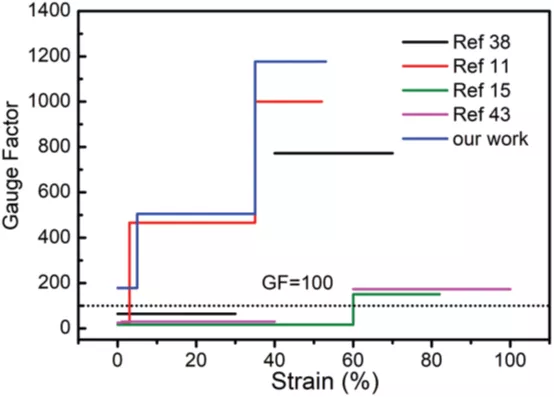
Figure 4. Comparison of sensor performance.
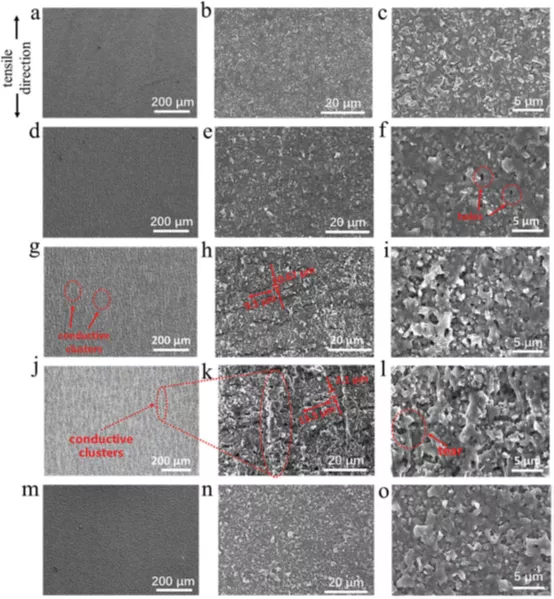
Figure 5. Top-view SEM images of the Ti3C2Tx conductive film in different stretched states during the first stretch release cycle.
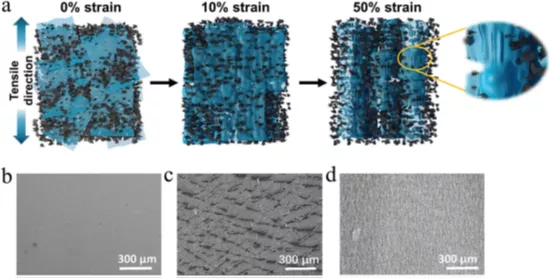
Figure 6. The whole drawing process of strain sensor based on Ti3C2Tx.
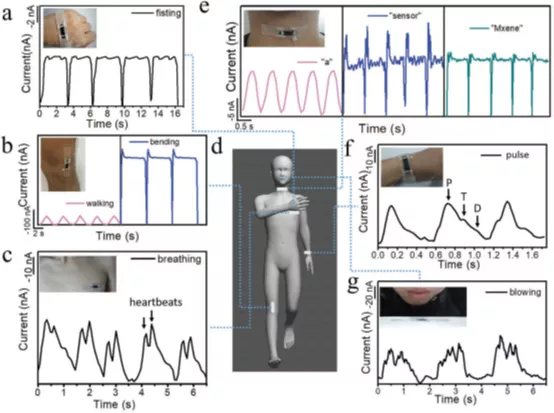
Figure 7. Response signal of Ti3C2Tx-based strain sensor when monitoring various physiological movements.
【Summary of this article】
This paper introduces a scalable strain sensor based on Ti3C2Tx nanoparticle-nanosheet composite conductive network, which has high sensitivity (>178.4), wide operating range (0 -53%), low detection limit (0.025%) and excellent Cycle durability (over 5000 cycles). Through the demonstration of the full range of human motion detection, it is verified that the hybrid network has high comprehensive performance. The cooperative movement of nanoparticles and nanosheets was discovered, and a mechanism of constrained microcrack propagation was proposed. The migration of nanoparticles creates holes and microcracks. Nanoflakes wrap and bridge the separated nanoparticles to limit the rapid propagation of microcracks, resulting in a significant change in resistance. The strain sensor based on the crack mechanism has high sensitivity, but because the rapid propagation of the crack will seriously damage the conductive path, its working range is usually narrow. The mechanism of constrained micro-crack growth proposed in this paper may be an ideal solution to this problem, and has some enlightening significance for the design of the microstructure of the sensing material and substrate.
Literature link:
In recent years, stretchable and wearable strain sensors have attracted a lot of attention in academia due to their advantages of portability, foldability, portability, and biocompatibility. Sensitivity (ie, strain factor (GF) and stretchability are two important parameters for evaluating the sensor performance of strain sensors. For small deformations, such as pulse and heartbeat, high sensitivity is required. At the same time, high stretchability is the detection The basis of a lot of body movements caused by joint movements. In general, in order to meet the basic requirements of full-range human motion detection, strain sensors must have a sensing range of more than 50% and a measurement coefficient greater than 100 in the full working range. However, the enhancement of sensitivity and the enhancement of the working range are contradictory, because sensitivity requires significant structural changes to occur at small strains, and stretchability requires the device to maintain the connectivity of the conductive path in the large strain area; therefore, manufacturing the ideal strain Sensors still face huge challenges.
【Achievement Introduction】
In 2019, Associate Researcher Wang Ranran and Researcher Sun Jing from the Shanghai Institute of Ceramics, Chinese Academy of Sciences published an article in the internationally renowned academic journal Advanced Functional Materials: Strain Sensors with a High Sensitivity and a Wide Sensing Range Based on a Ti3C2Tx ( MXene) Nanoparticle–Nanosheet Hybrid Network research paper successfully constructed a unique Ti3C2Tx nanoparticle-nanosheet composite network for strain sensors, which has a high sensitivity (GF>) in the full range (0-53%) 178.4), very low detection limit (0.025%) and good cycle durability (over 5000 cycles). The coordinated movement of Ti3C2Tx nanoparticles and nanosheets is the main reason for their excellent comprehensive performance. Three different sensing stages and constrained micro-crack growth mechanisms were discovered. When stretched, the migration and separation of the nanoparticles cause a large resistance change, and the nanoflakes wrap and bridge the separated nanoparticles, maintaining the connectivity of the conductive path in a large strain area. Different proportions of Ti3C2Tx nanoparticles and nanosheets show the diversity of structure and morphology in the hybrid network, which helps to fully functionalize the microstructure and maximize the synergistic effect. The Ti3C2Tx hybrid network shows quite high sensitivity to sensors based on a single nanoparticle or flake, but its working range has been expanded by 7-10 times.
In addition, demonstrations of human activity detection from precise speech recognition to violent human movements have confirmed the superiority of hybrid networks.
【Graphic introduction】
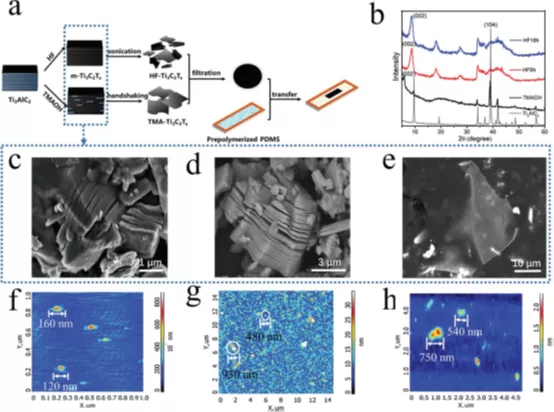
Figure 1. Ti3C2Tx synthesis and characterization.
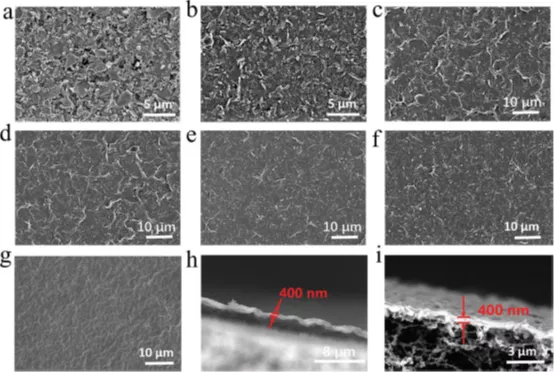
Figure 2. SEM image of Ti3C2Tx conductive film.
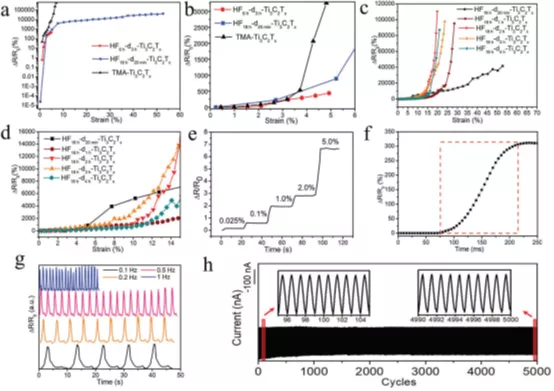
Figure 3. Strain sensing characteristics of a strain sensor based on Ti3C2Tx.
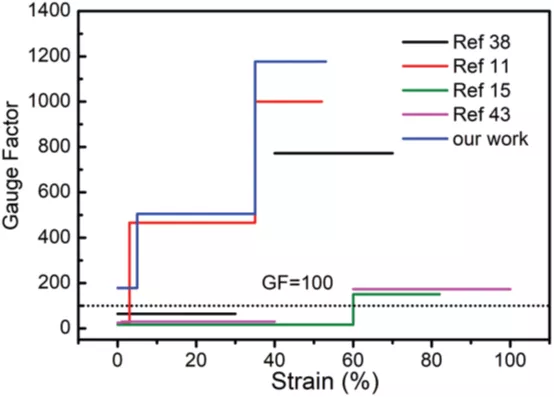
Figure 4. Comparison of sensor performance.
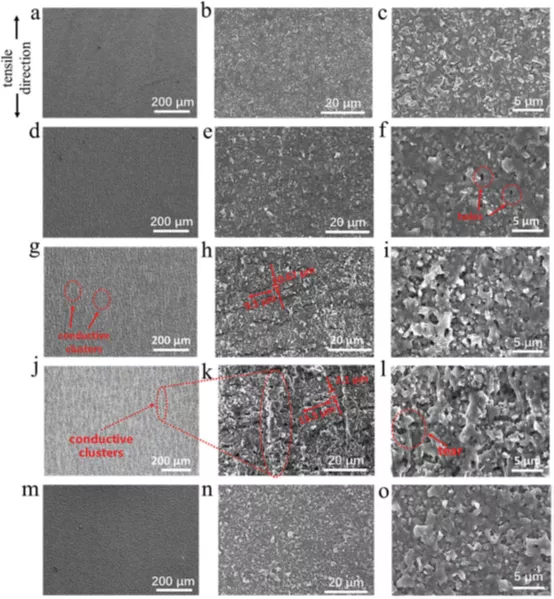
Figure 5. Top-view SEM images of the Ti3C2Tx conductive film in different stretched states during the first stretch release cycle.
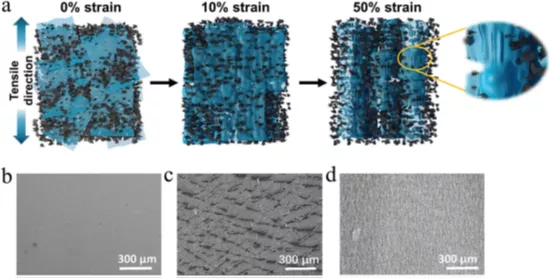
Figure 6. The whole drawing process of strain sensor based on Ti3C2Tx.
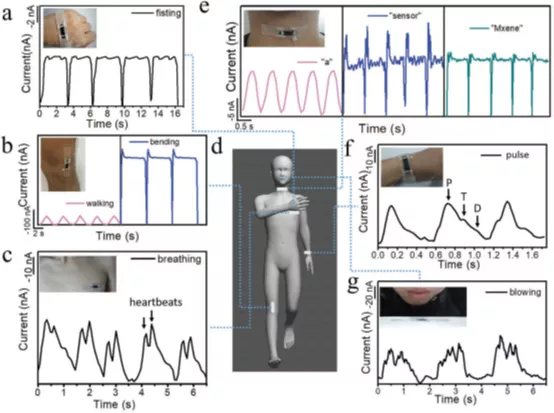
Figure 7. Response signal of Ti3C2Tx-based strain sensor when monitoring various physiological movements.
【Summary of this article】
This paper introduces a scalable strain sensor based on Ti3C2Tx nanoparticle-nanosheet composite conductive network, which has high sensitivity (>178.4), wide operating range (0 -53%), low detection limit (0.025%) and excellent Cycle durability (over 5000 cycles). Through the demonstration of the full range of human motion detection, it is verified that the hybrid network has high comprehensive performance. The cooperative movement of nanoparticles and nanosheets was discovered, and a mechanism of constrained microcrack propagation was proposed. The migration of nanoparticles creates holes and microcracks. Nanoflakes wrap and bridge the separated nanoparticles to limit the rapid propagation of microcracks, resulting in a significant change in resistance. The strain sensor based on the crack mechanism has high sensitivity, but because the rapid propagation of the crack will seriously damage the conductive path, its working range is usually narrow. The mechanism of constrained micro-crack growth proposed in this paper may be an ideal solution to this problem, and has some enlightening significance for the design of the microstructure of the sensing material and substrate.
Literature link:
https://doi.org/10.1002/adfm.201807882.
Source: MXene Frontie
This information comes from the Internet for academic exchange only. If there is any infringement, please contact us to delete it immediately
- Previous: AEM review: MXenes for
- Next: MXene breakthrough: Na